Pallet Block Machine For Wooden Packaging Production Plant
Sawdust block making machine | Wooden block press machine
Pallet Block Machine For Wooden Packaging Production Plant
Sawdust block making machine | Wooden block press machine
Features at a Glance
The wood pallet block machine is an efficient solution for recycling wood waste. It’s user-friendly, allowing one operator to manage three machines simultaneously. The standard sizes for pallet blocks include 80*80 mm, 90*90 mm, 90*120 mm, and 100*100 mm. If you have specific needs, we can customize sizes from 75 mm to 145 mm. The final product can achieve a density of 550-1000 kg/m³.
With a daily capacity of 4-5 cubic meters of raw material, the machine can be tailored with molds to create blocks that fit particular size and shape specifications. The end product is primarily used for protecting items, absorbing vibrations, filling gaps, or providing support, and it finds applications in the construction, packaging, and transportation sectors.
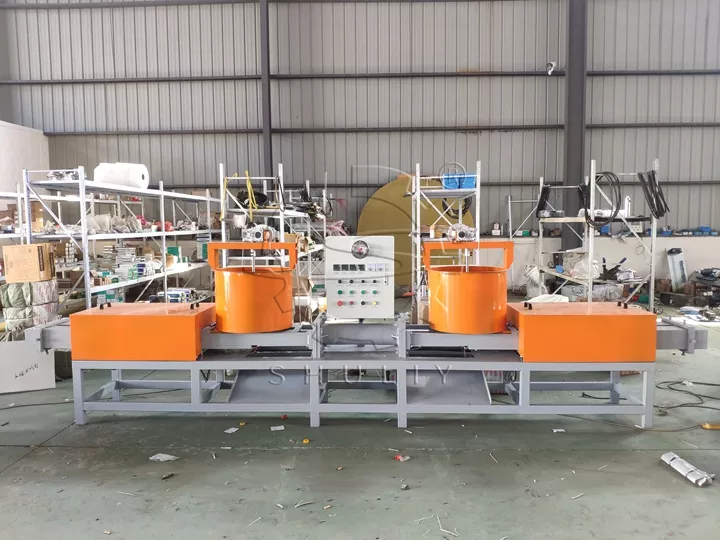
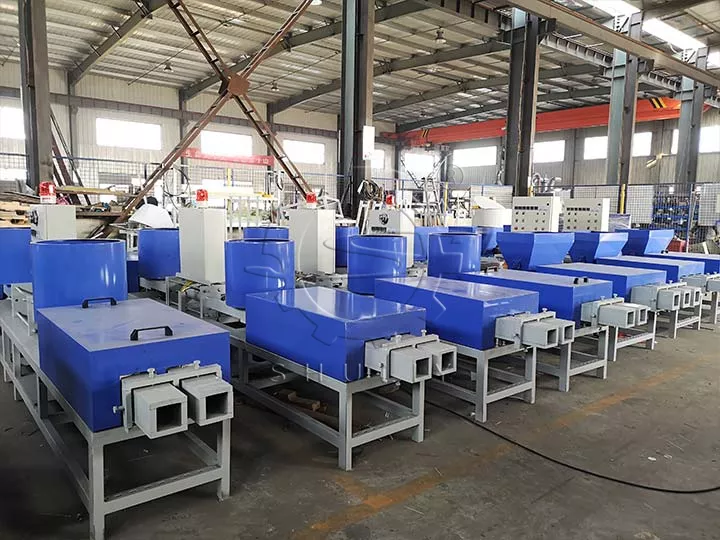
Raw materials of pallet block machine
The feedstock for this machine is about three to five millimeters in size and is usually sawdust that has been through a wood crusher or hammer mill crusher. The shavings have been through a wood shaver machine. Alternatively, the raw materials may include some rice hulls and woodchips.
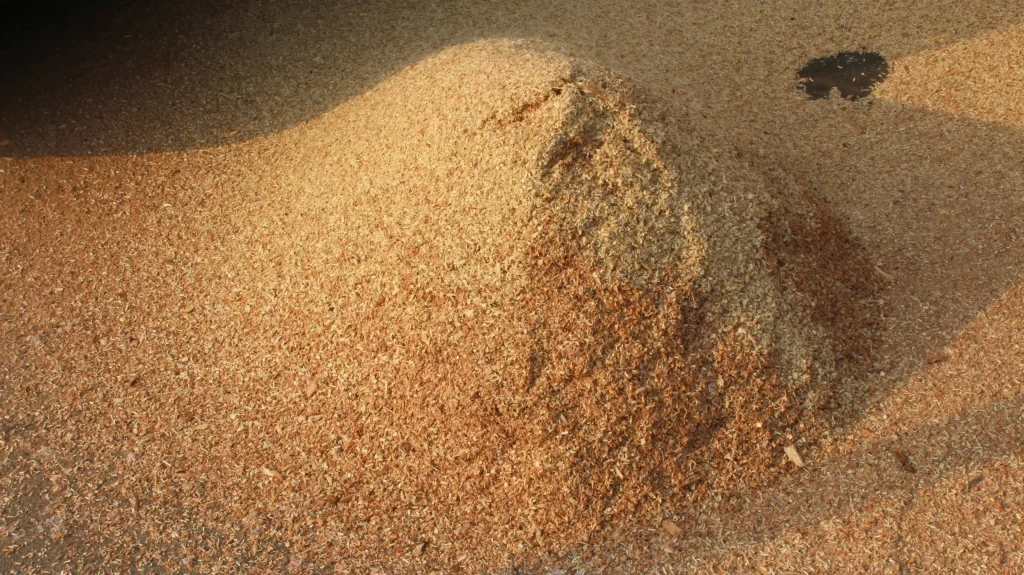
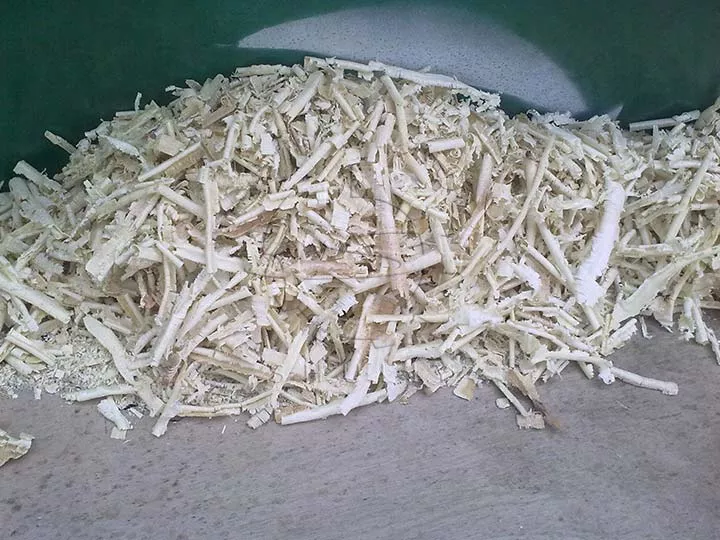
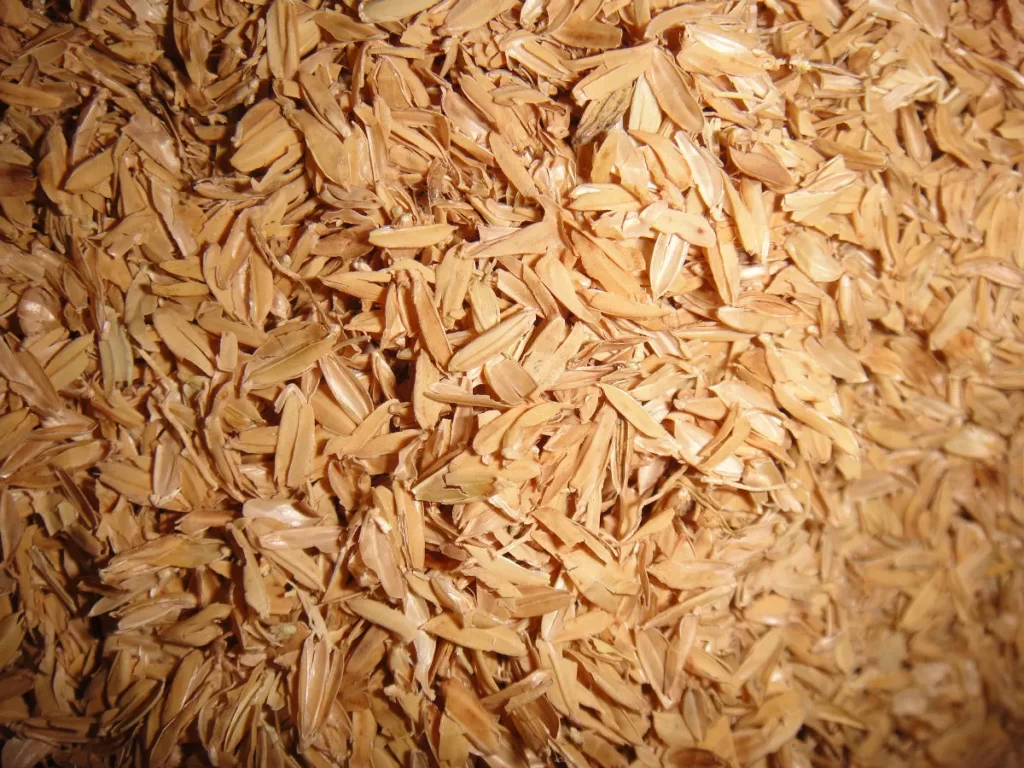
Sawdust block machine finished production and application
Pallet block machines are widely used in many different fields, mainly for producing various types of blocks to meet the needs of different industries. Pallet blocks can be solid, with no hole in the middle, or hollow.
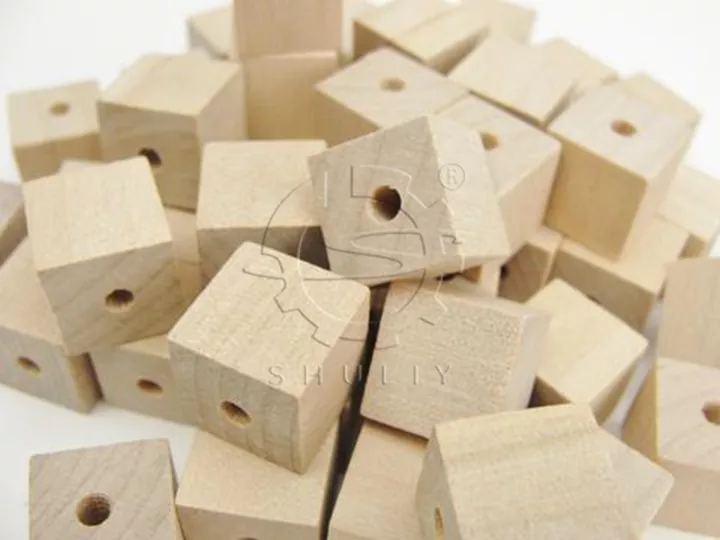
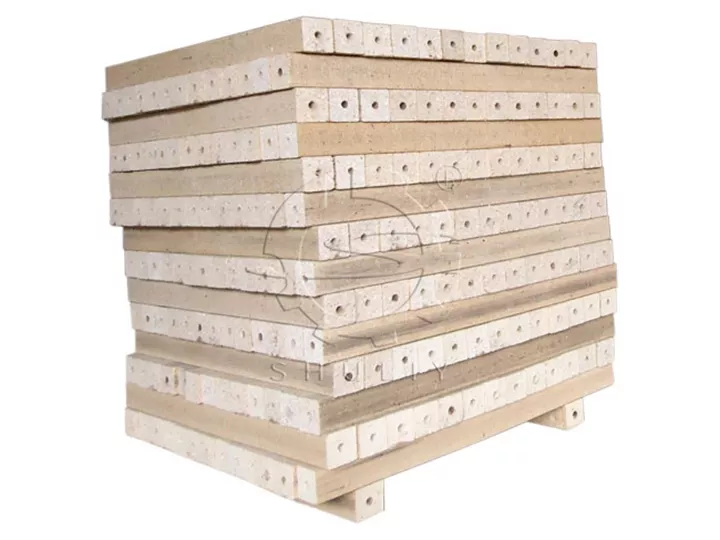
- Packing industry: materials like foam padding and bubble wrap are utilized to safeguard products from damage while they are being transported or stored.
- Industrial protection: pallet blocks can be designed to shield industrial equipment, parts, and products by minimizing vibration, absorbing impacts, and protecting surfaces.
- Transportation industry: this machine is capable of producing padding blocks specifically for cargo transportation and loading, ensuring that the cargo remains secure and undamaged during transit.
- Furniture manufacturing: the machine can create padded cushions, including seat and back cushions, which are essential in the furniture manufacturing process.
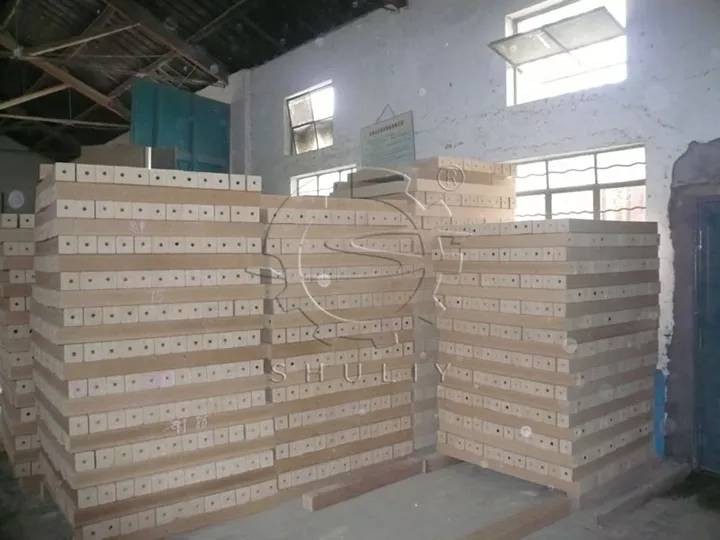
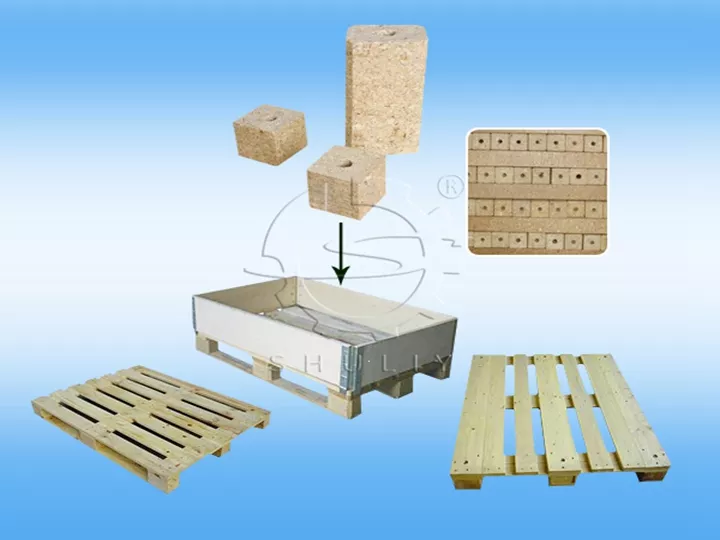
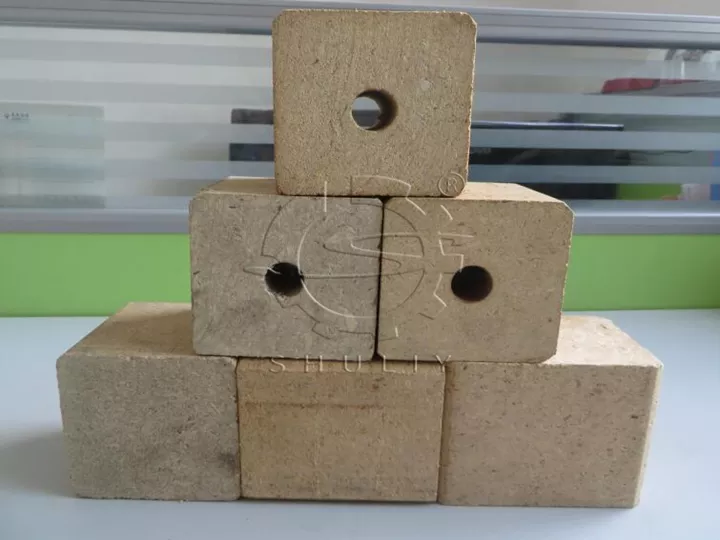
Wood block forming machine features
- The pallet block machine is designed to handle various types, shapes, and sizes of raw materials, allowing for the production of a wide range of matting products tailored to different customer needs.
- With an automated production process, the machine lessens the labor intensity for operators and enhances the overall comfort of the working environment.
- Additionally, the molds and settings of the machine can be easily adjusted and swapped out to accommodate different products, providing a level of production flexibility.
- Since the blocks are extruded and molded at high temperatures, fumigation is not required.
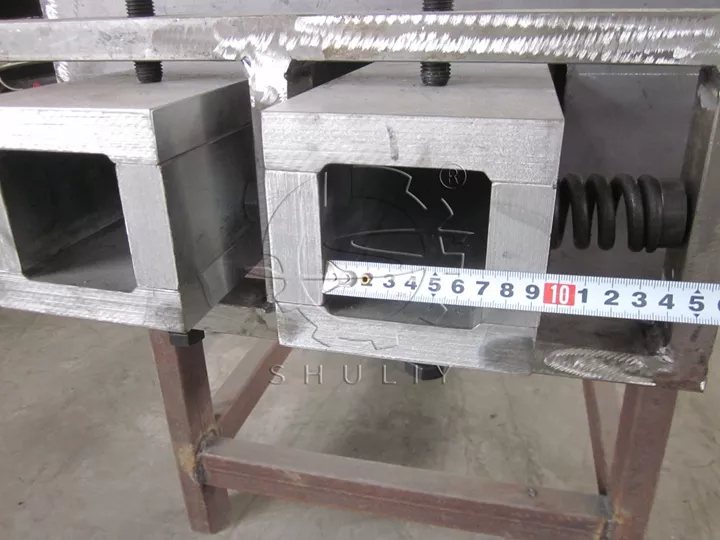
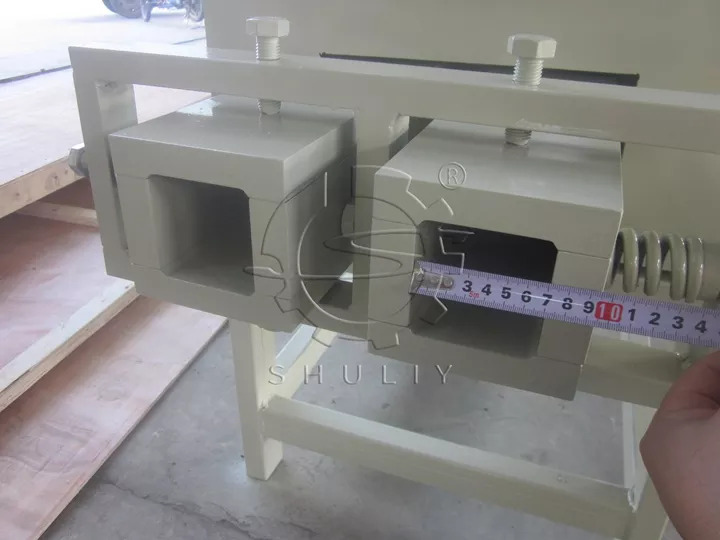
How does pallet block press machine work?
The pallet block machine transforms raw materials into mat blocks of specific shapes and sizes by following several steps: supplying raw materials, heating, molding, cutting, cooling, and collecting. Various models of briquetting machines may employ different technologies and mechanisms throughout these steps to cater to the production requirements of different block types.
The hydraulic cylinder generates high pressure to drive the piston, shaping the material as it is extruded.
The heating plate reaches elevated temperatures to facilitate the curing and molding of urea-formaldehyde glue.
Cutting is performed to a specific length, typically around 1.2 meters.
Once cooled, the semi-finished long wood strips are trimmed to their final dimensions.
Additionally, the long wood strips can be processed into blocks of various sizes using a cutting machine, if desired. The equipment operates at a speed of 1800 blocks per hour.
Wood pallet block production line
Wood crusher → selection of raw materials → dryer(Controlling the moisture content of raw materials to less than 12%.) → glue mixer → feed mixing drum → heater → molding cylinder → cutting machine.
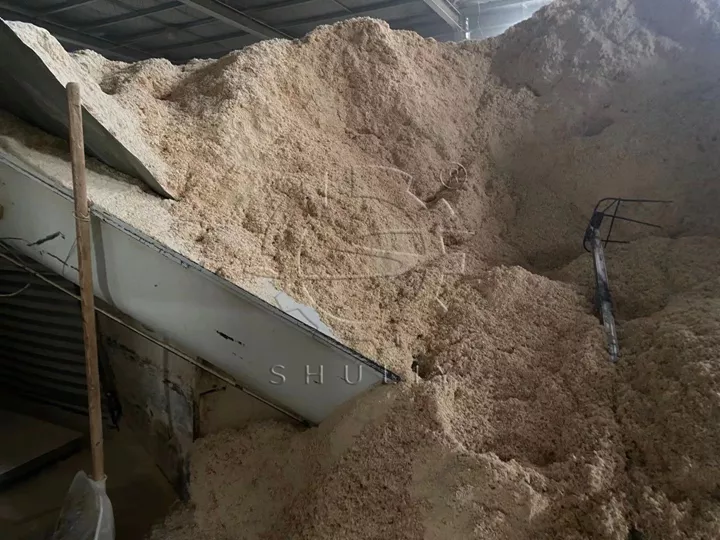
Raw materials: to choose appropriate materials, this process must consider the size and moisture content of the raw materials. As a result, the selected raw materials should first be placed in a dryer to reduce the moisture level to below 12 percent.
Glue mixer: to increase the density of the finished product, the raw material needs to be mixed with glue, which is usually urea-formaldehyde resin glue. The purpose of this is to make the finished product stronger and have more load-bearing capacity.
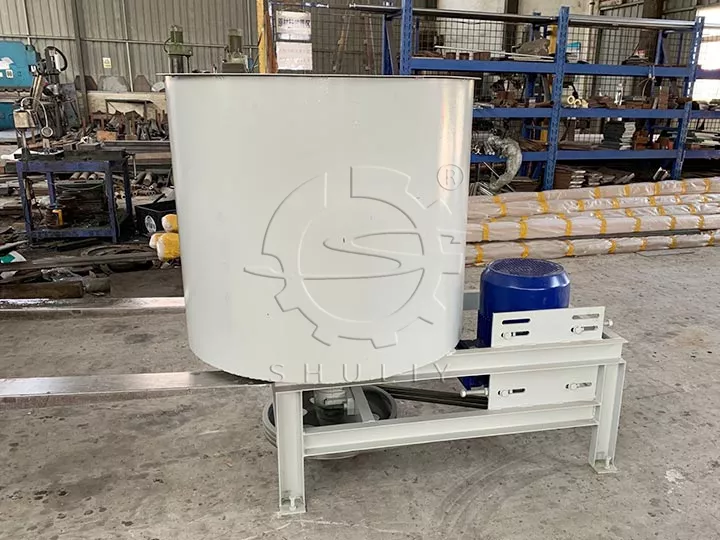
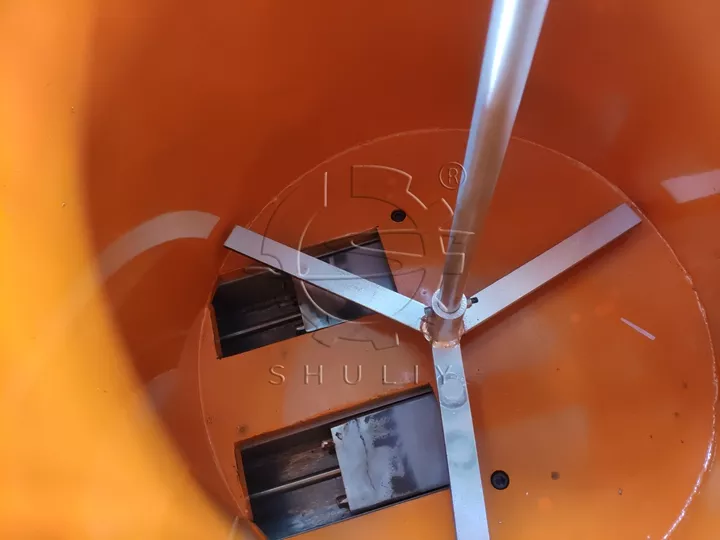
Feed mixing drum: when feeding, it is essential to include a stirring device in the feeding cylinder to prevent the solidification of the raw materials mixed with glue. This also helps to ensure that the materials are more uniform.
Heating device: raw materials are heat and pressure treated to melt or expand and heat molded.
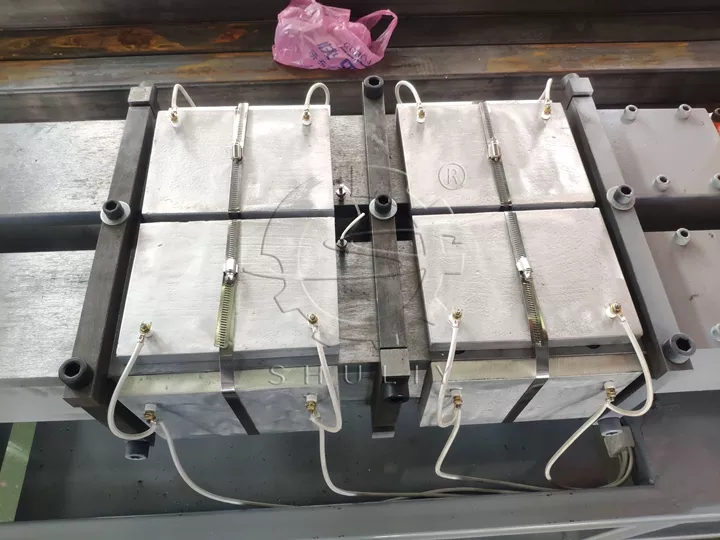
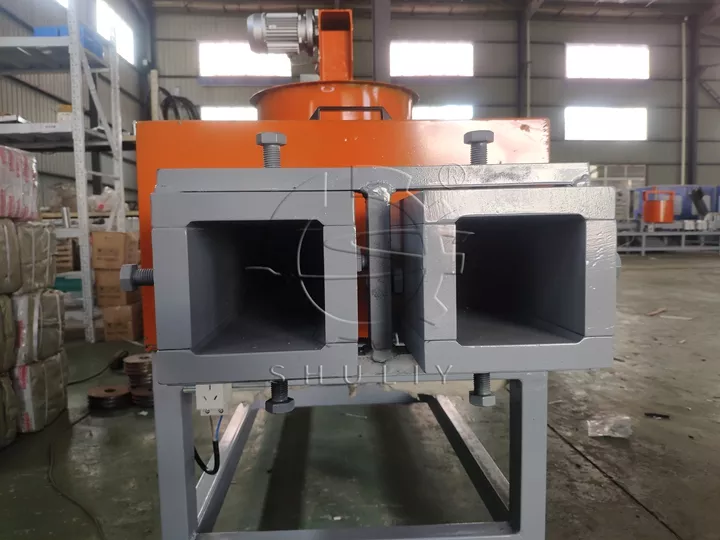
Molding cylinder: the material is formed using a mold. The dimensions and shape of the pads are dictated by the various models of molding cylinders. Typical sizes include 75×75, 80×80, 90×90, 90×120, 100×100, 100×115, 100×140, and 140×140 mm.
Pallet block cutting machine: the newly formed blocks are cooled to cure and stabilize them. They are then cut into the desired individual pieces or combinations of pieces using a cutting or separating device.
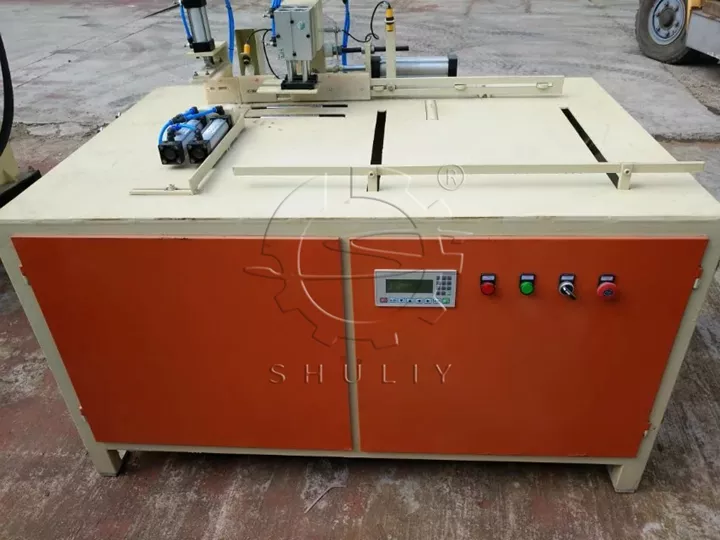
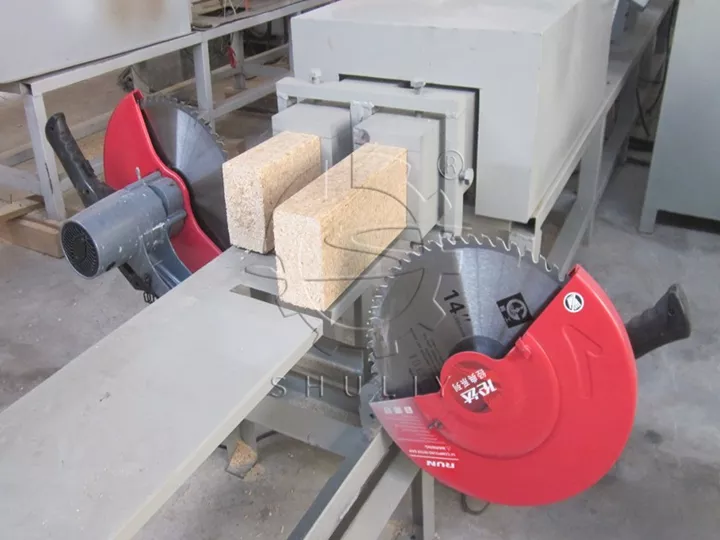
Knife-cutting device: in addition to using a block cutter, you can also attach a stand and two cutters for block cutting directly at the back of the molding cylinder.
Presswood block molding machine model parameters
Recently, our company successfully shipped to Indonesia one set of pallet block production line machines, the following are the technical parameters of the pallet block machine.
Dimension(mm) | Weight(kg) | Final product(mm) | Capacity(m³/24h) |
4800*760*1300 | 1200 | 70*90 | 4-5 |
Temperature control method: PID power regulation and voltage regulation control
Overall, pallet block machines play an important role in many different fields, providing key solutions for product protection, packaging, transportation, and performance. Due to the wide range of demands for matting, the application areas for wood block making machines are also very diverse. If you are interested, please feel free to contact us.
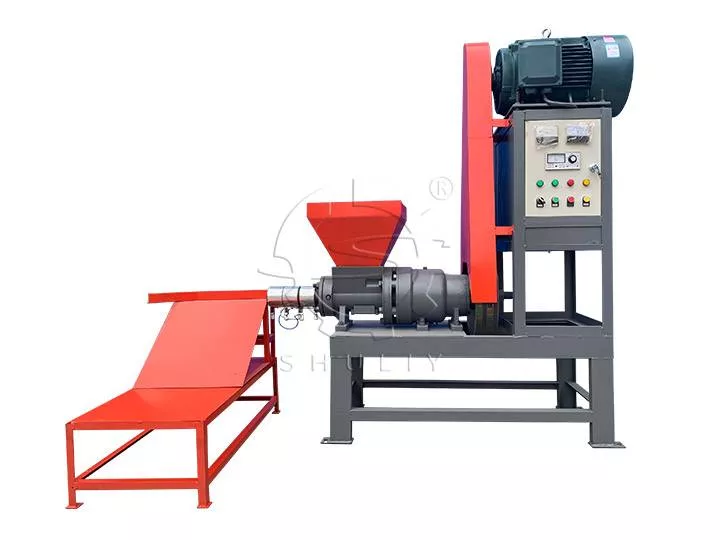
Sawdust Briquette Machine For Biomass Charcoal Processing Line
The sawdust briquette machine is designed to compress waste materials…
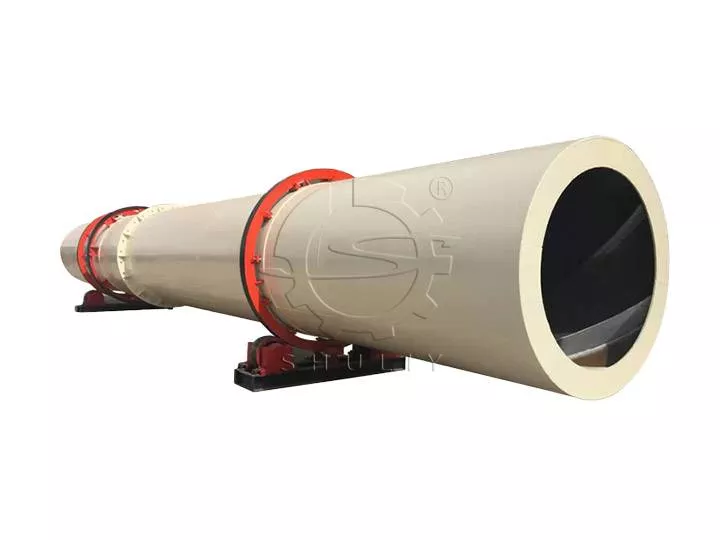
Rotary Drum Dryer Machine For Sawdust Powder Drying Plant
The rotary drum dryer machine is commonly used to evaporate…
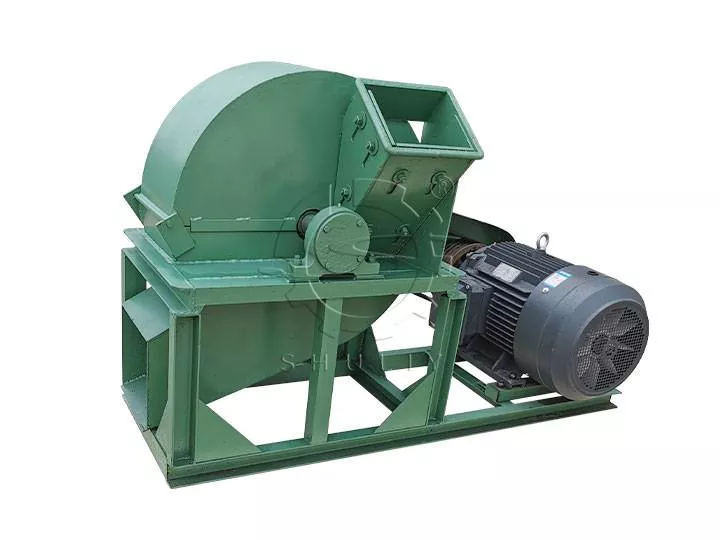
Wood Crusher Machine For Making Sawdust
The wood crusher machine features high-speed rotating knives and a…
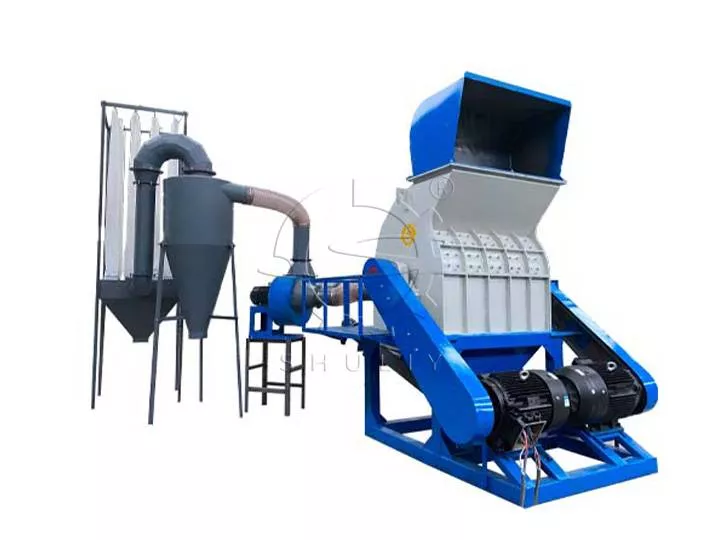
Large Hammer Mill Crusher in Sawdust-making Plant
The wood hammer mill crusher operates by using the high-speed…
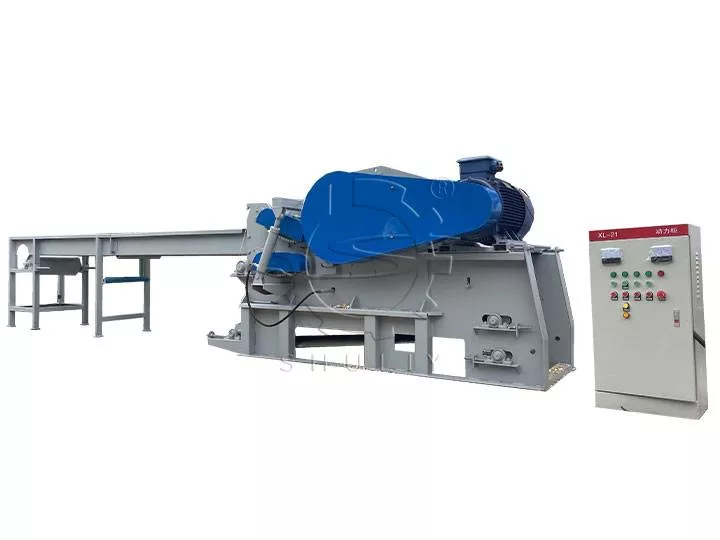
Wood Chipper Machine For Sawdust-making Plant
The wood chipper machine is designed to break down wood,…
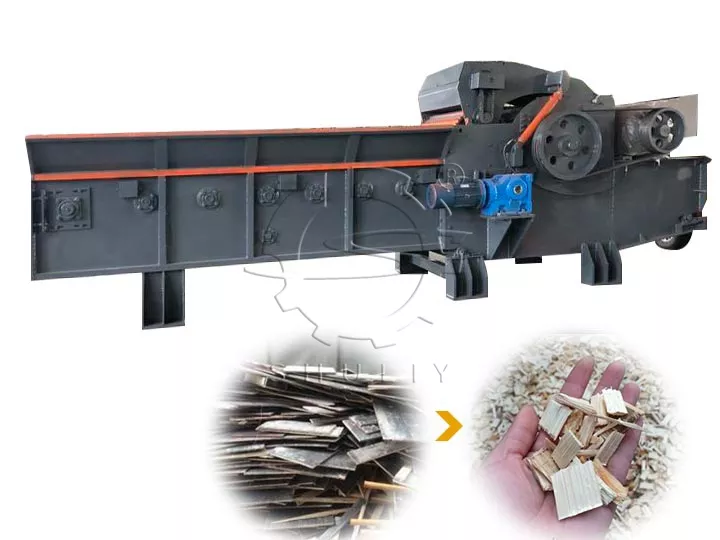
Comprehensive Crusher Large Capacity Wood Shredder Machine
The comprehensive crusher is designed to break down large pieces…
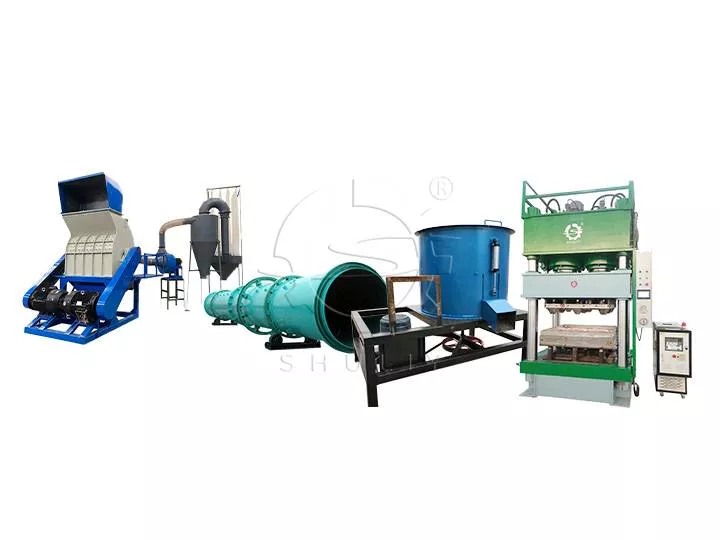
Presswood Pallet Production Line For Wood Recycling Plant
The presswood pallet production line is dedicated to making molded…

Automatic Compressed Wood Pallet Blocks Production Line For Sale
The wood pallet blocks production line uses waste wood chips,…
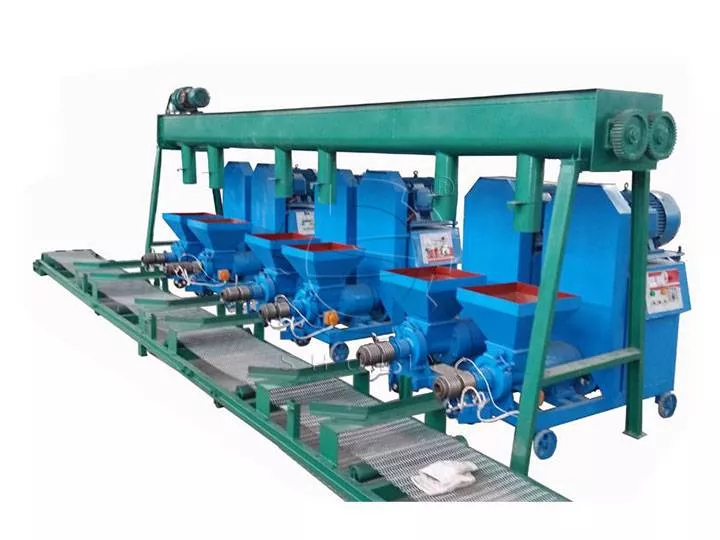
Sawdust Briquettes Production Line Pini Kay Making Machines
The sawdust briquettes production line processes raw materials such as…
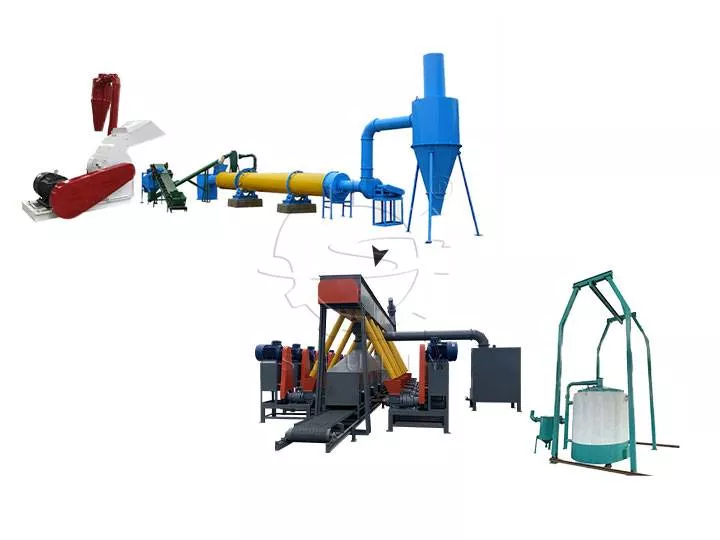
Sawdust Charcoal Production Line For Biomass Processing Plant
The sawdust charcoal production line takes wood, wood chips, or…
Hot Product
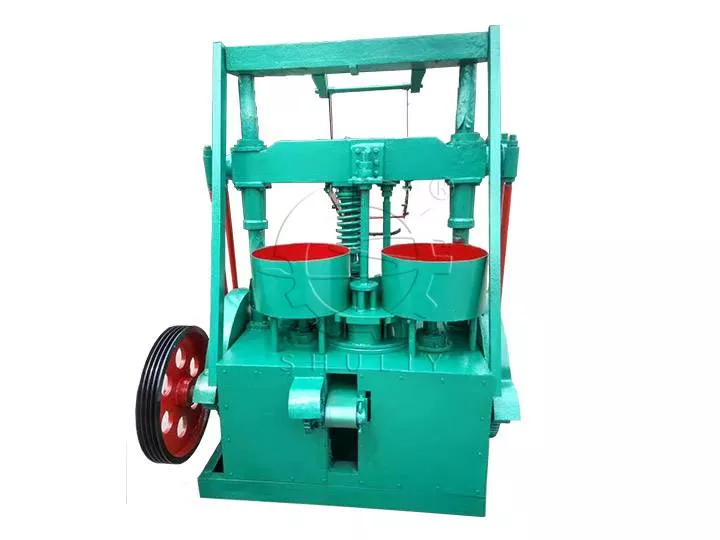
Honeycomb Coal Machine For Briquette Forming Production Line
Honeycomb coal machine regards well-processed coal dust as…
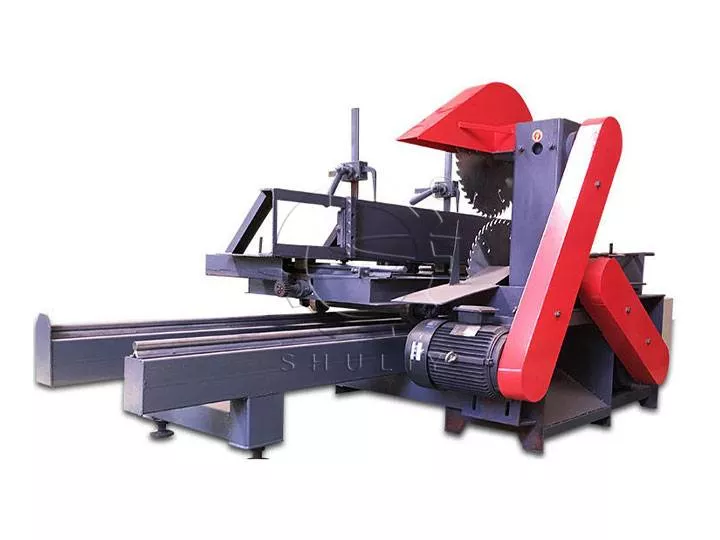
Automatic Saw Mill Machine For Wood Recycling Plant
The saw mill machine cuts larger logs into…
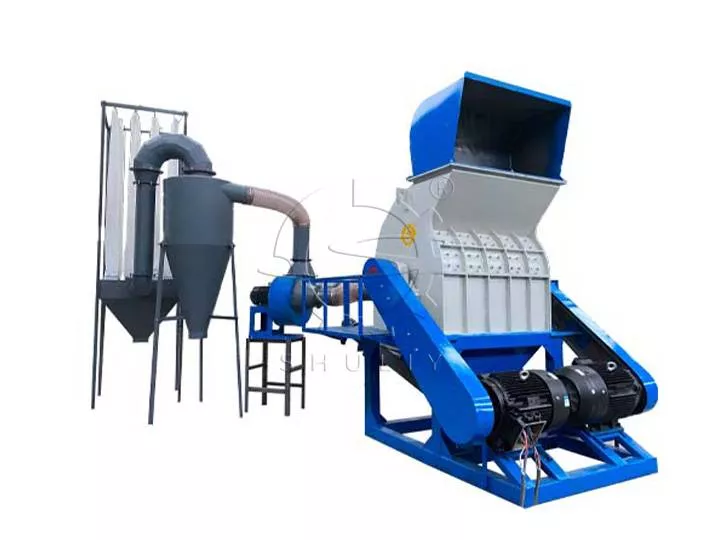
Large Hammer Mill Crusher in Sawdust-making Plant
The wood hammer mill crusher operates by using…
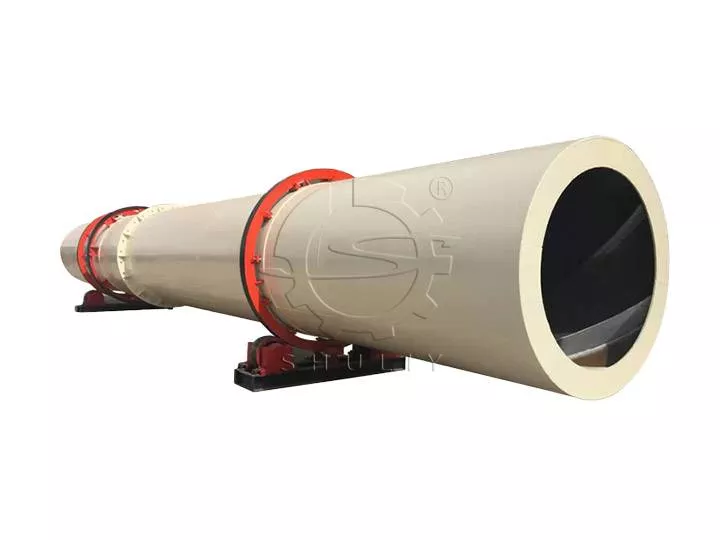
Rotary Drum Dryer Machine For Sawdust Powder Drying Plant
Rotary drum dryer machine is a common industrial…
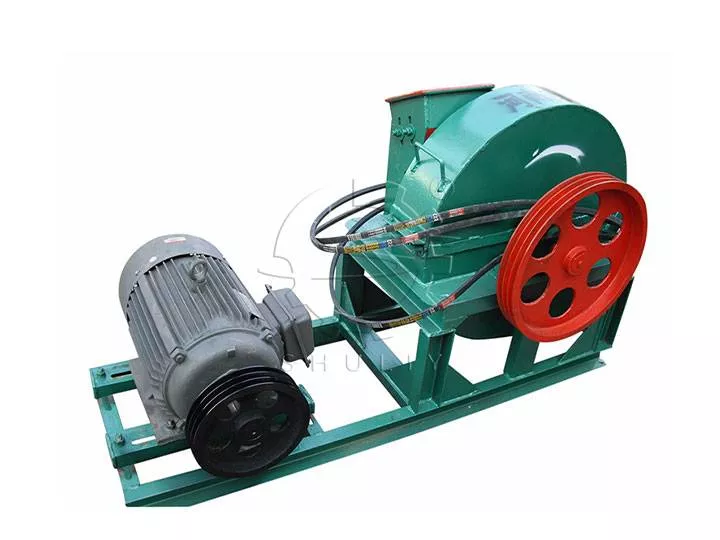
Wood Shaving Machine For Animal Bedding
The wood shaving machine is designed to process…
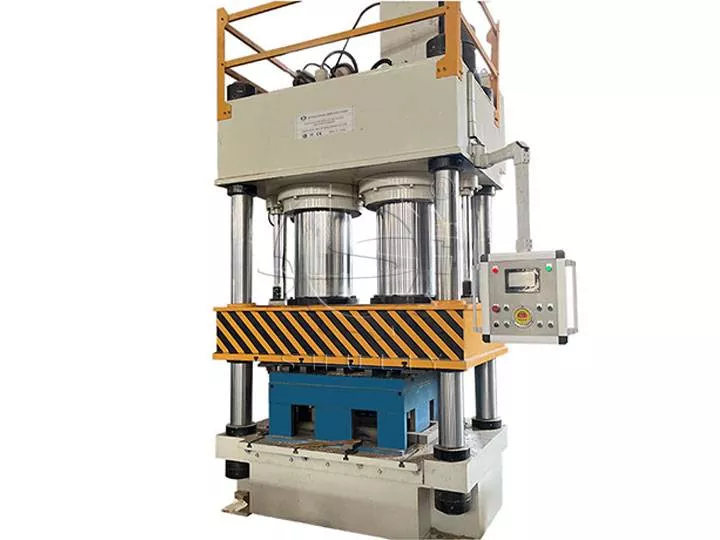
Automatic Wood Pallet Press Machine For Sale
Wood pallet press machine mainly process compressed wooden…
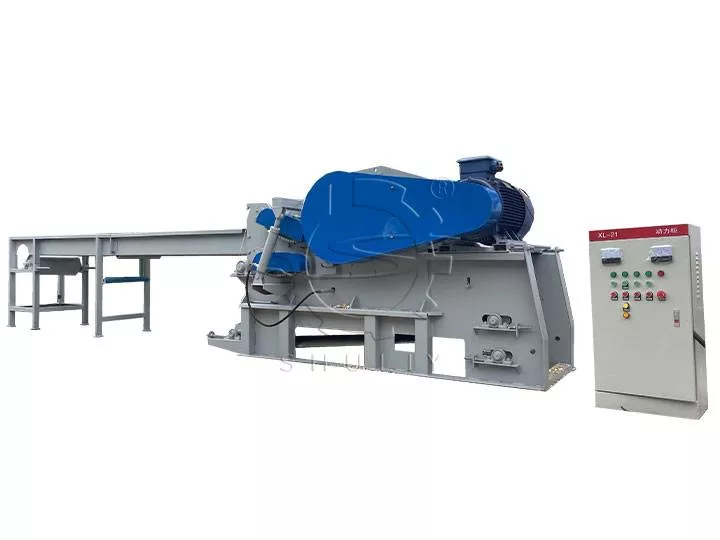
Wood Chipper Machine For Sawdust-making Plant
The wood chipper machine is designed to break…
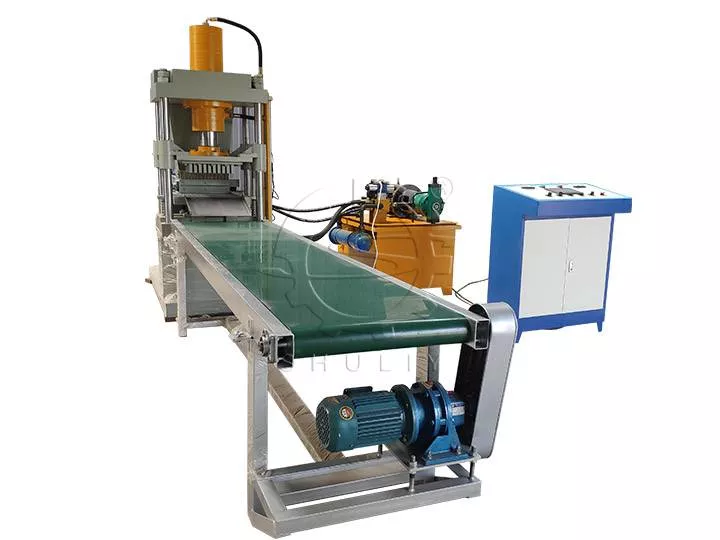
Hydraulic Shisha Charcoal Briquette Machine For Coal Forming
Hydraulic shisha charcoal briquette machine is also a…
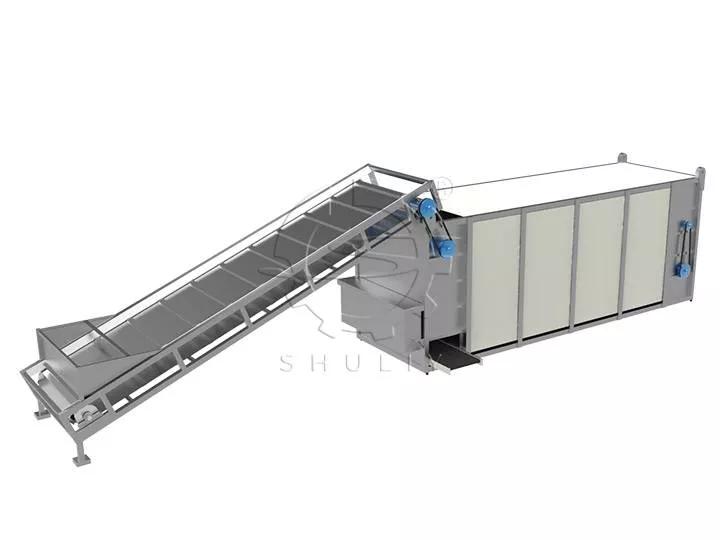
Charcoal briquette mesh belt dryer for continuous drying plant
Charcoal briquette mesh belt dryer is a continuous…