Automatic Compressed Wood Pallet Blocks Production Line For Sale
Automatic Compressed Wood Pallet Blocks Production Line For Sale
The wood pallet blocks production line uses waste wood chips, wood shavings, or various straws containing wood fibers as raw materials. After a series of processing, the block products are widely used in the logistics and transportation industry.
We can customize the mold of the compressed wood block machine according to the customer’s requirements for pallet size specifications. The block size is usually 75*75mm, 80*100mm, 80*120mm, 90*90mm, 90*140mm, 100*100mm, 100*115mm, 100*140mm, 140*140mm, etc.
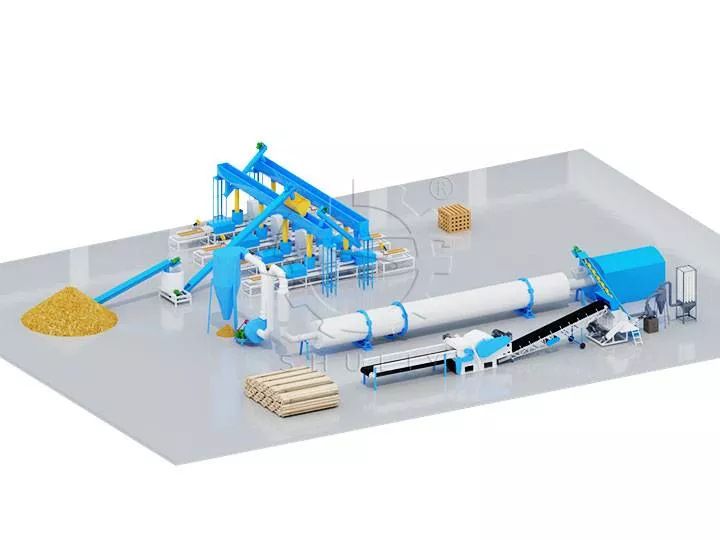
Raw materials for making wood pallet blocks
The raw materials used to make wood bedding blocks are mainly waste wood which are by-products of wood products. These raw materials can be leftovers from wood processing, furniture manufacturing, building construction, etc., which are processed and reused to make wood cushion blocks.
The following are some of the common raw materials used to make wood matting blocks: wood chips and sawdust, wood shavings, bamboo, and so on. The larger sizes of these wood chips can be cut, crushed, and processed to make the raw materials suitable for wood briquettes.
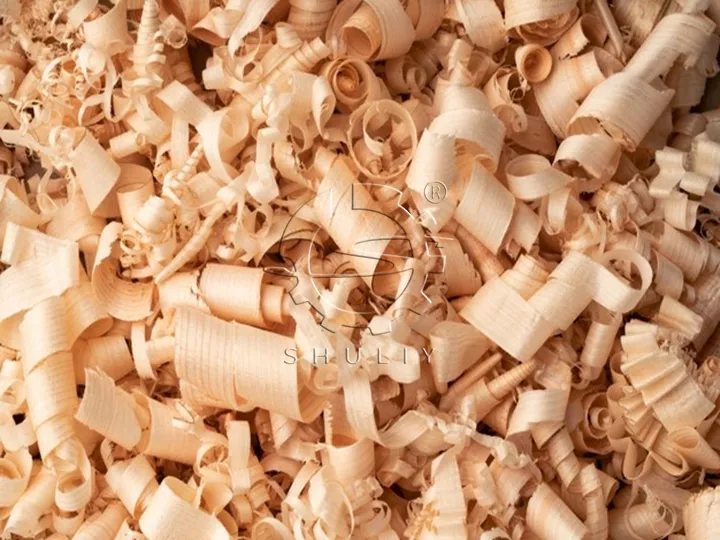
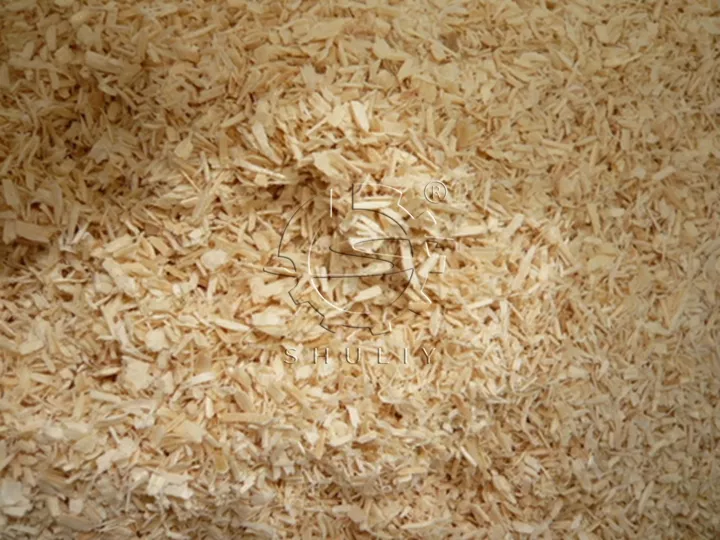
Usage of finished wood pallet block
The main use of wood pallet blocks is in the manufacture of wood pallets. Pallet blocks are the main support structures or stringers of the pallet. They are usually located at the corners or edges of the pallet and provide strength and stability. Pallet blocks are assembled with other components such as deck boards and nails to form a complete pallet.
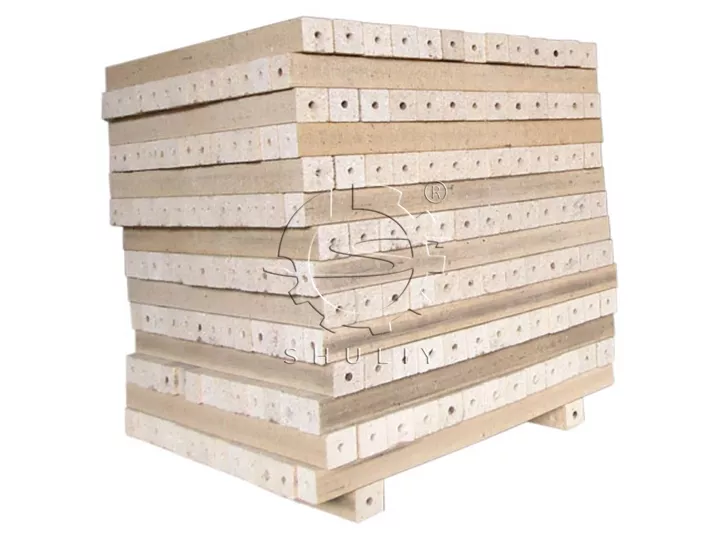
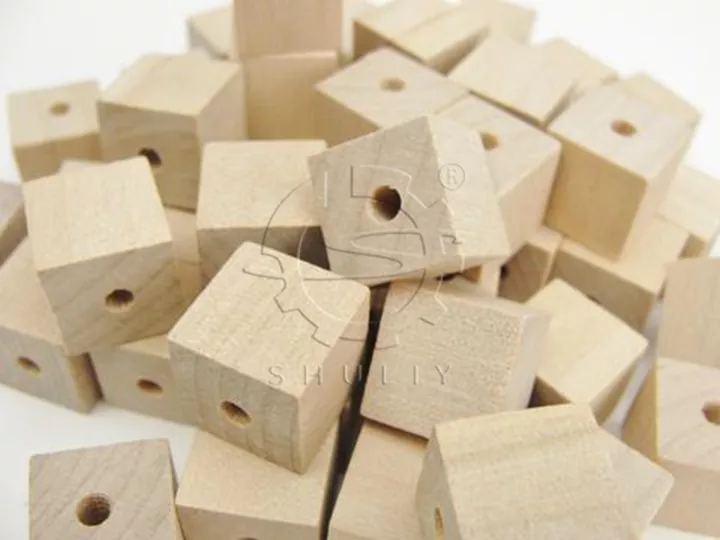
Who invested in this production line?
- Lumber or sawmill businesses: Waste wood materials can be reused to produce valuable products, reducing waste disposal costs and maximizing resource utilization.
- Pallet manufacturers: Existing wooden pallet manufacturers who want to expand production capacity or improve efficiency can invest in an automated wood pallet blocks production line. It can streamline operations, increase production, and reduce labor costs.
- Entrepreneurs and startups: It lays the foundation for establishing a new pallet manufacturing business because key processes are automated. This reduces initial labor requirements and enables efficient production from the start.
- Recycling and waste management companies: Wood waste or byproducts from operations can be used as raw materials for the production of pallet blocks. Generate additional revenue streams by converting waste into value-added products such as pallet blocks.
Complete sawdust pallet block production line structure
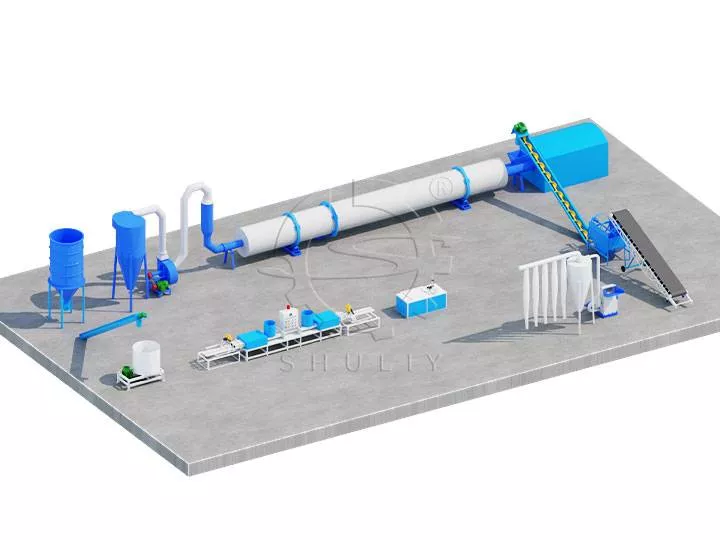
In the process of the whole wood pallet blocks production line for making wood blocks, the following machines are mainly included and are carried out in order:
Drum wood chipper machine→Hammer mill crusher→Screening machine→Screw conveyor→Rotary drum dryer→Glue mixer→Conveyor→Pallet block machine→Cutting machine.
Among them, the cutting device is optional equipment, customers can choose whether to buy this equipment according to the demand and budget and so on.
Workflow of wood pallet blocks production line
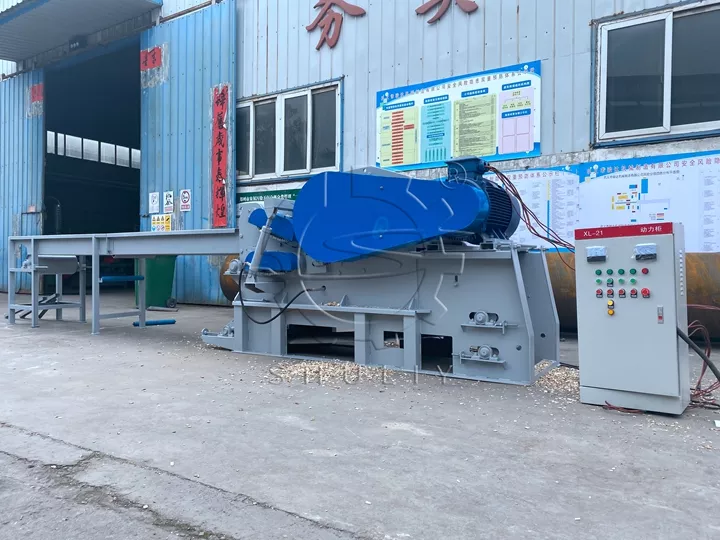
Drum wood chipping machine: In the wood pallet blocks production line with larger output, the drum chippers pulverize larger-sized wood or wood chips into fine particles using a rotating drum and blades.
The raw materials are evenly cut and crushed into relatively consistent particle sizes, ensuring uniform and consistent quality of the finished matting.
Hammer mill crusher: Hammer blade pulverizer also plays an important role in mat block production line, similar to a drum chipper, which is mainly used in the stage of further crushing and breaking down of raw materials to obtain granular raw materials suitable for making wood mat blocks. The sawdust size usually needs to be controlled at 3-5mm.
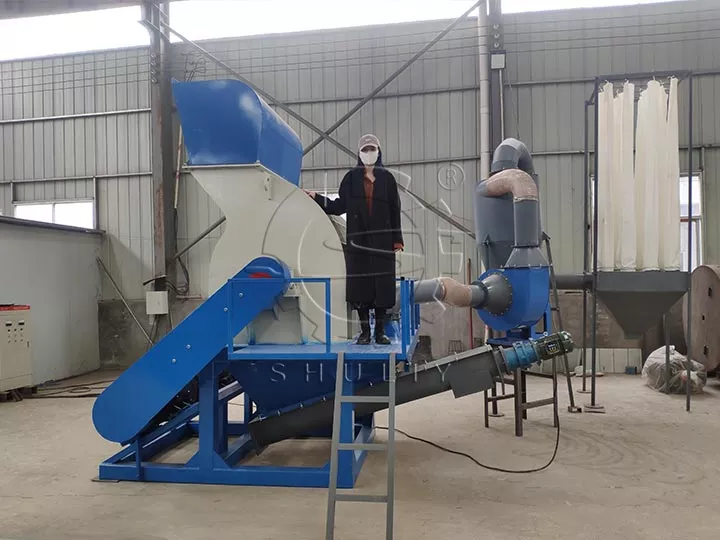
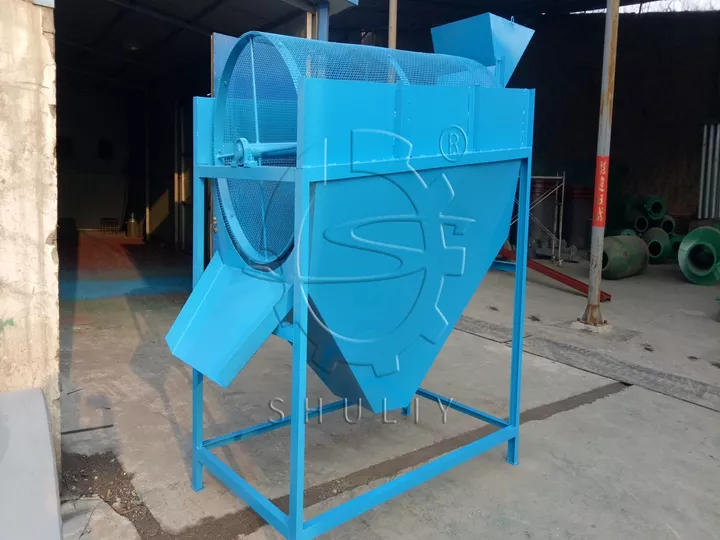
Screening machine: It can classify the raw materials after the crushing and breaking process according to different particle sizes.
It can remove impurities, fragments, and foreign materials from the raw materials to ensure that only the particles that meet the standard are selected, improving the quality of the products.
Screw conveyor: Screw conveyor has an important role in the wood pallet blocks production line, which can continuously convey the raw materials from the feeding end to the discharging end to ensure the stable operation of the production line. It reduces the manual intervention and improves the production efficiency.
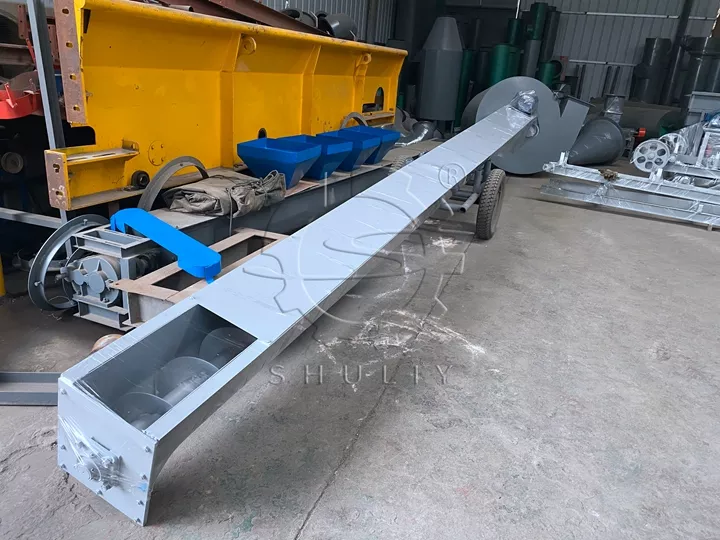
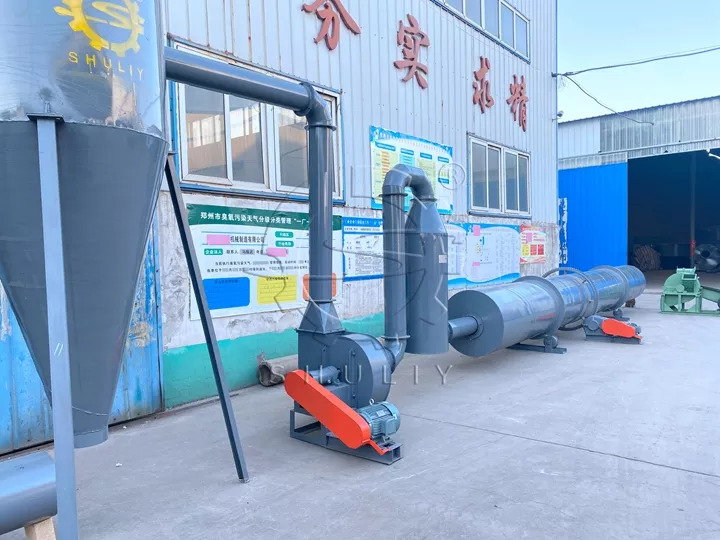
Rotary drum dryer machine: The moisture of the raw material for making woodblock needs to be controlled below 12%, the drum dryer can evaporate the moisture in the block so that the processed cushion block becomes dry. Improve the stability and quality of matting and maintain hygiene.
Glue mixer: By rotating the mixing blades, the glue mixer evenly mixes the urea-formaldehyde resin adhesive into the wood chips, thus improving the bonding strength and stability of the produced mat blocks.
Since this device has a limited volume and works in batches, it is possible to purchase more than one unit to reduce wait times.
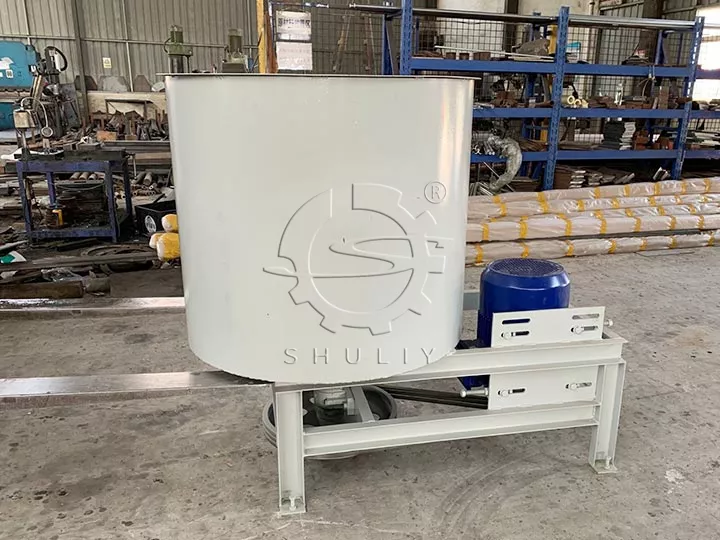
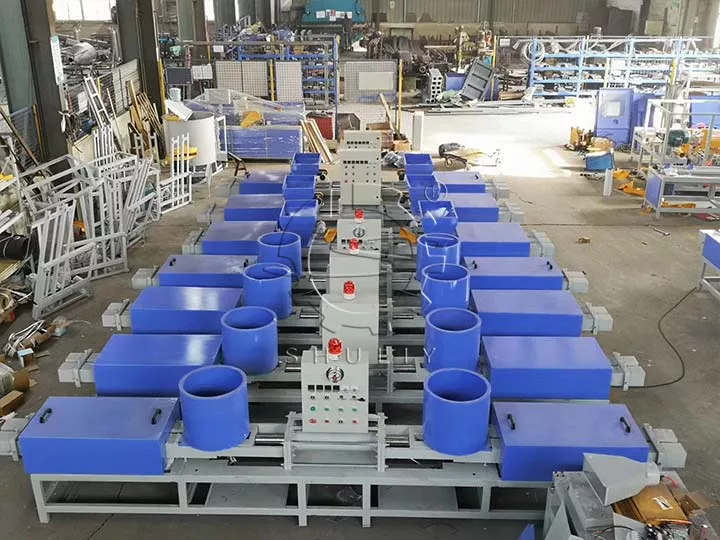
Wood pallet block machine: Once the raw material is ready, it can be transported to the briquetting machine with a conveyor, or if the budget is low, manual loading is also an option.
The raw material is processed in this machine by heating and molding. You can click this article Pallet block machine for wooden packaging production plant to learn how it works.
Dicing machine: The finished product from the pallet block machine can be stacked and packaged in cubes for sale.
This optional equipment can also be selected for further block-dicing processing. The finished products obtained in these two forms are shown in the figure below.
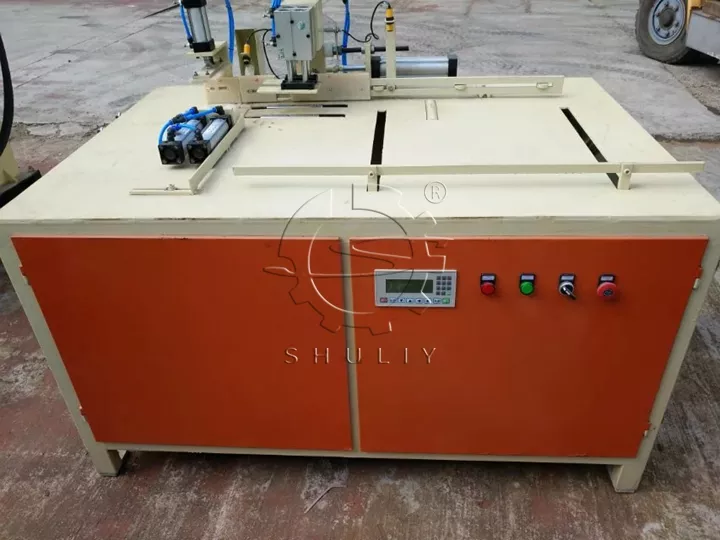
How to efficiently make wooden blocks?
After the above series of processes, you can get the desired wooden block product. The following is a working video showing the wood pallet blocks production line process.
Advantages of wood blocks making line
The wood pallet blocks production line has various advantages, which make it widely used in the field of wood mat block manufacturing. Following are some of the major features:
- This wooden pallet block production line specializes in producing wooden pallet blocks with or without holes, to recycle waste wood and make a profit.
- The raw materials used in this automatic wooden pallet production line are the same as those of the wooden pallet processing production line, so it is waste recycling.
- In the fully automatic wooden pallet production line, the entire production process from raw materials to the final product does not require direct worker participation in the operation. All production processes are completed by mechanical equipment and automation systems.
- The wooden blocks are produced with high temperature and high pressure, with common standards and European standards, and can also be customized according to customer needs.
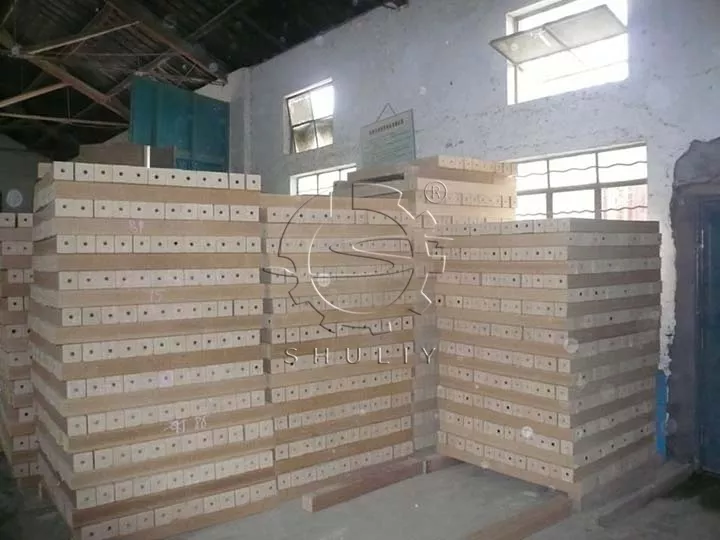
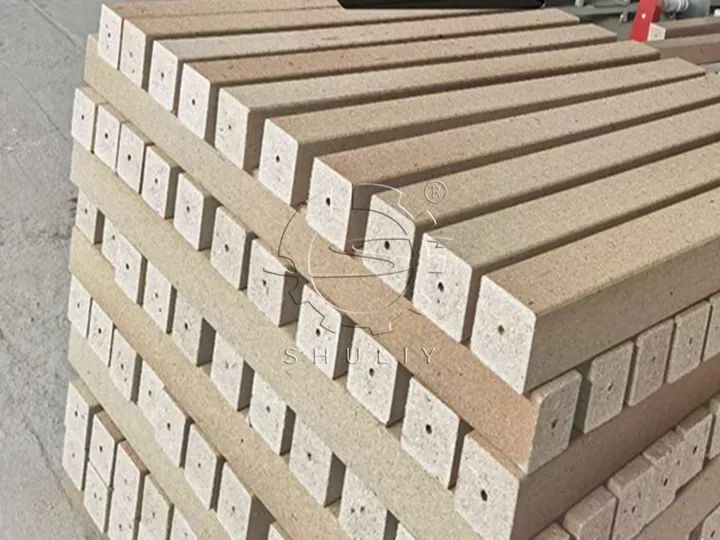
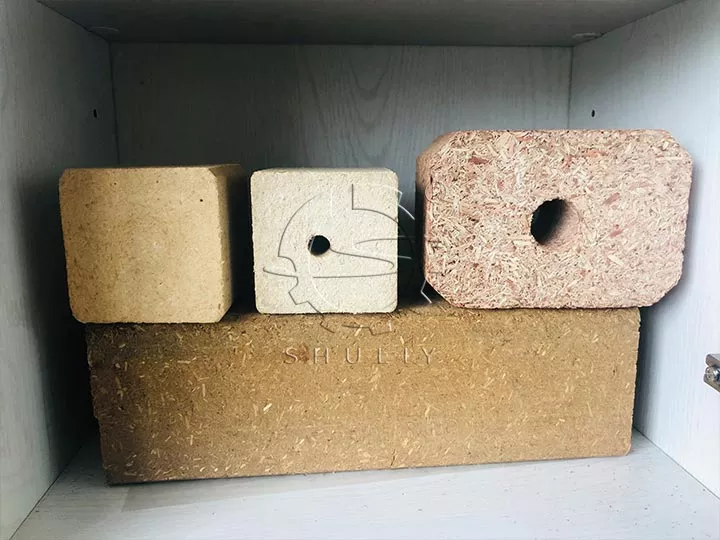
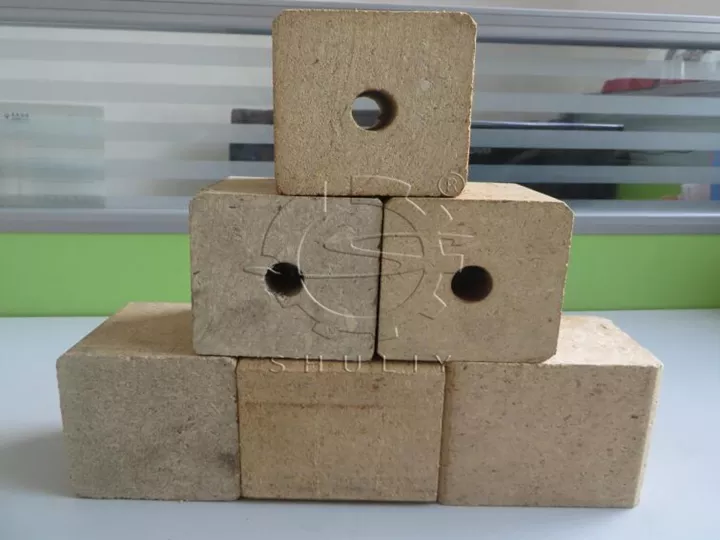
Customizable for different solutions
Please note that the above is only the basic conventional configuration plan of our company’s wood pallet blocks production line, we can customize different models according to your budget, requirements on output, and finished product size.
In addition, according to the local labor cost, we can also set up automatic or semi-automatic wood pallet blocks production lines. If you want to know more information, please feel free to contact us.
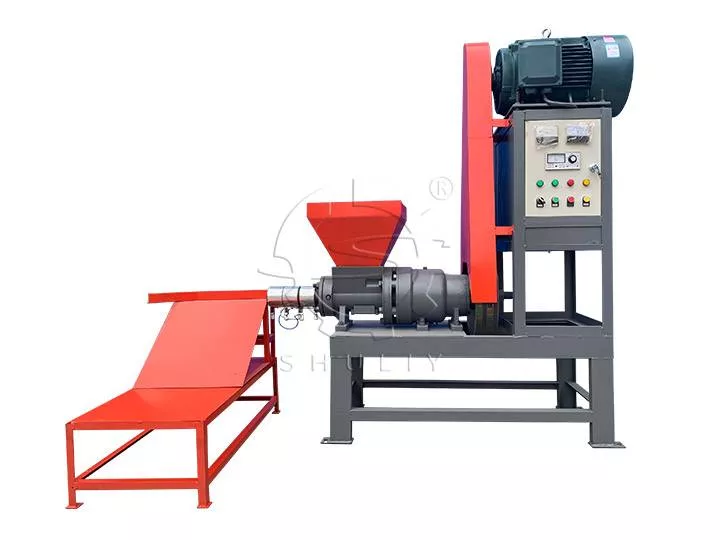
Sawdust Briquette Machine For Biomass Charcoal Processing Line
The sawdust briquette machine is designed to compress waste materials…
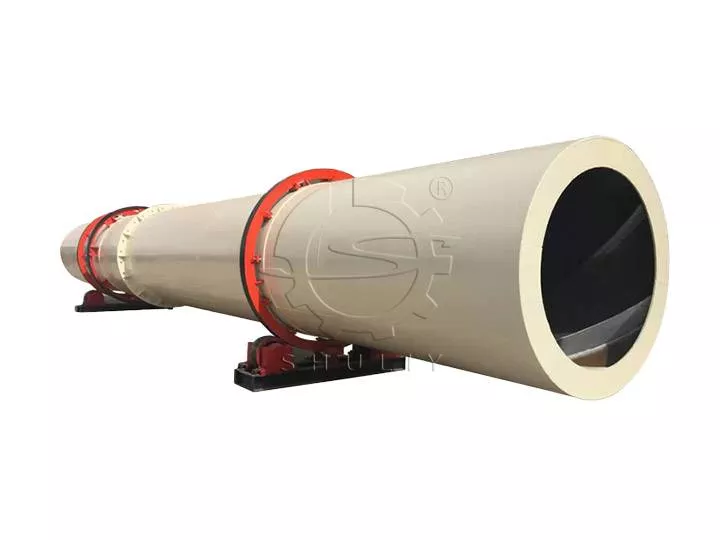
Rotary Drum Dryer Machine For Sawdust Powder Drying Plant
The rotary drum dryer machine is commonly used to evaporate…
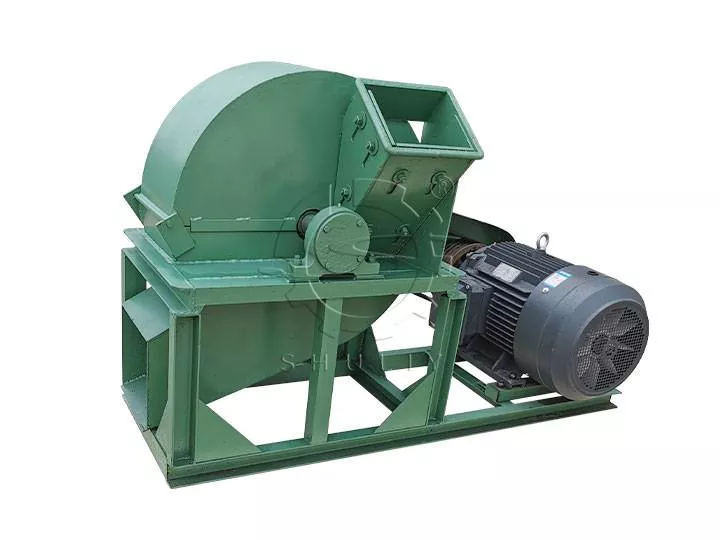
Wood Crusher Machine For Making Sawdust
The wood crusher machine features high-speed rotating knives and a…
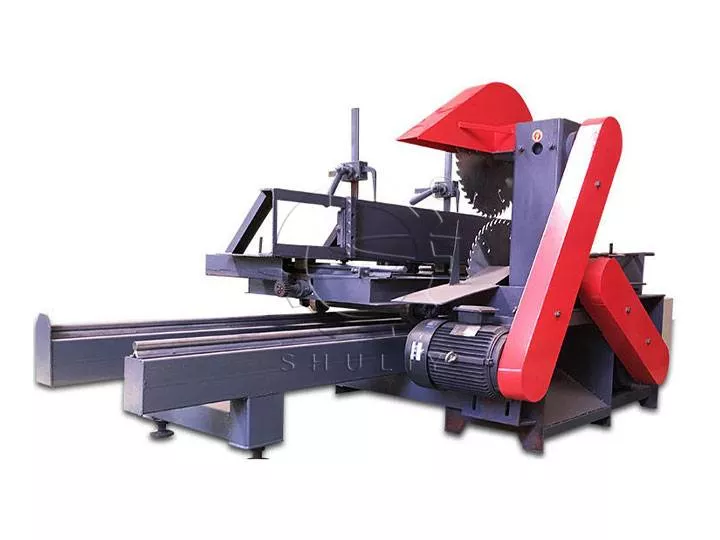
Automatic Saw Mill Machine For Wood Recycling Plant
The saw mill machine uses either a circular or band…
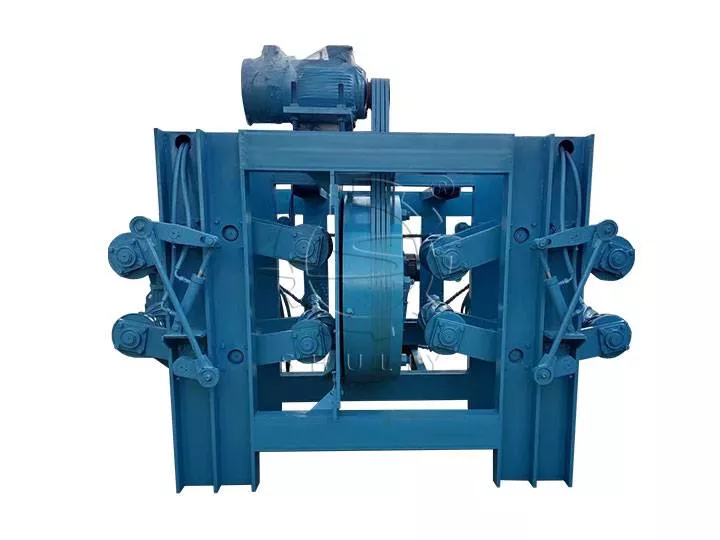
Wood Debarker Machine Timber Log Peeling Equipment
The wood debarker, equipped with high-strength alloy blades and advanced…
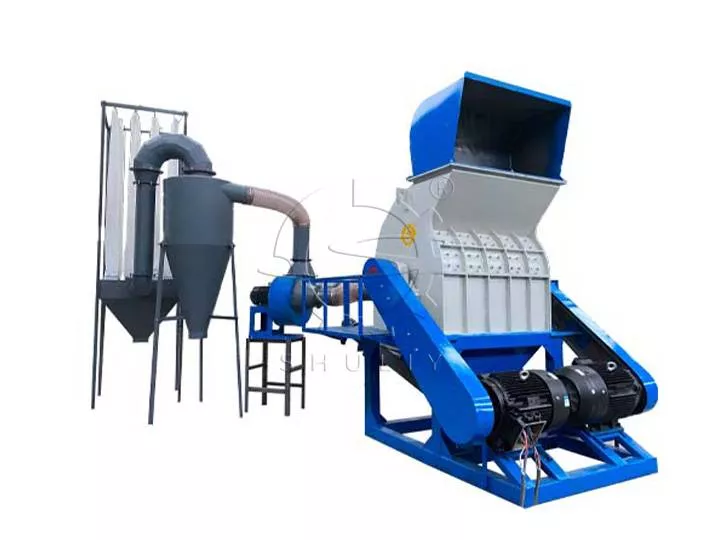
Large Hammer Mill Crusher in Sawdust-making Plant
The wood hammer mill crusher operates by using the high-speed…
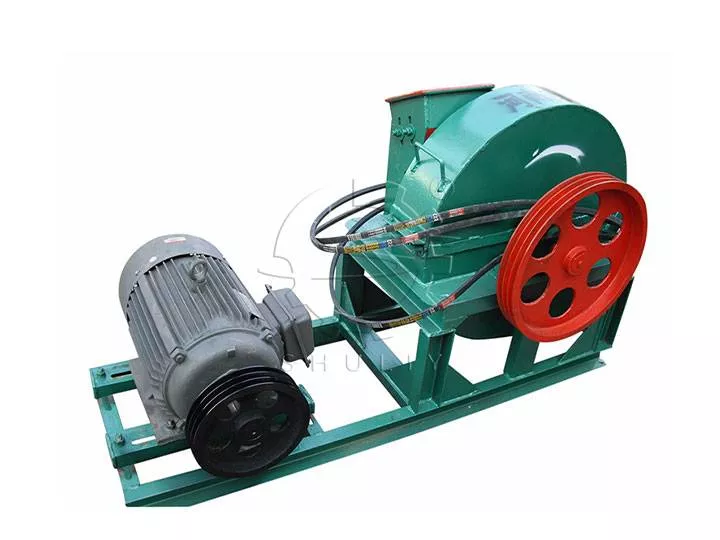
Wood Shaving Machine For Animal Bedding
The wood shaving machine is designed to transform wood of…
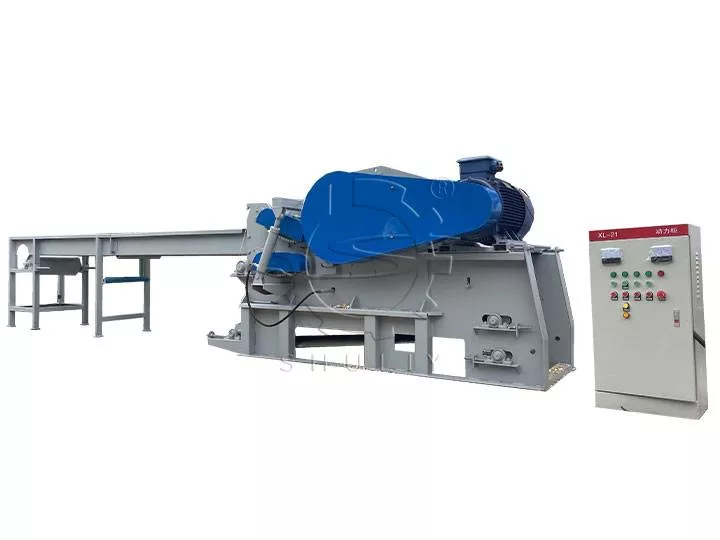
Wood Chipper Machine For Sawdust-making Plant
The wood chipper machine is designed to break down wood,…
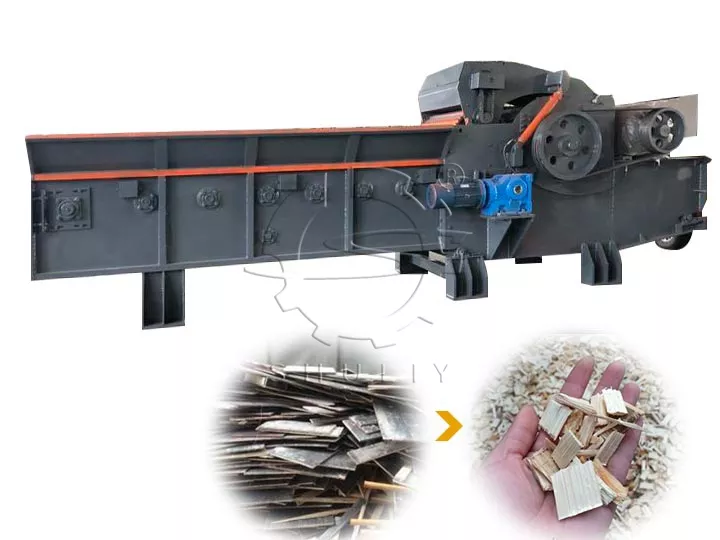
Comprehensive Crusher Large Capacity Wood Shredder Machine
The comprehensive crusher is designed to break down large pieces…
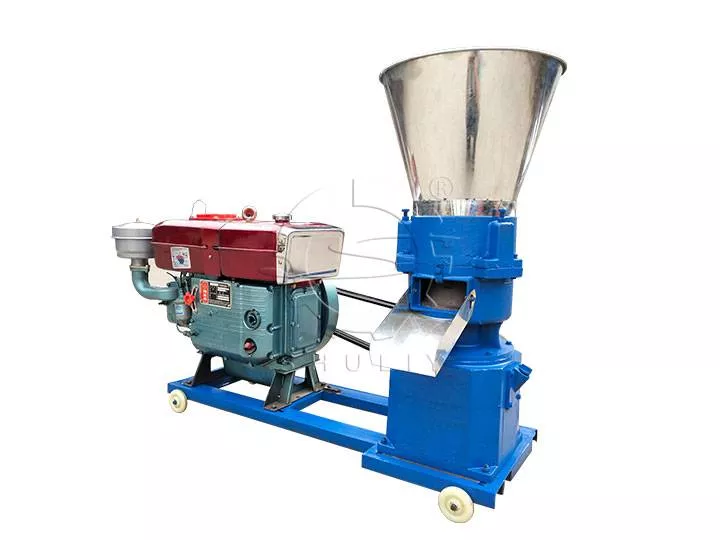
Feed Pellet Mill Machine For Animal Livestock
The feed pellet mill machine is a kind of equipment…
Hot Product
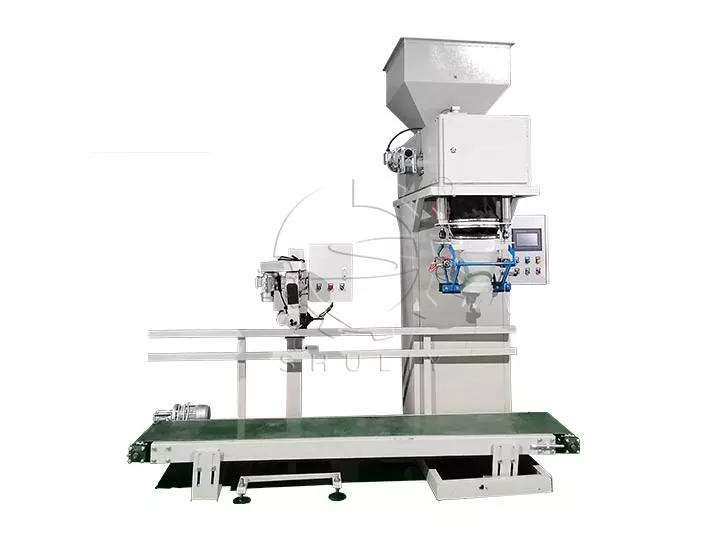
BBQ Charcoal Packing Machine in Briquette Production Line
A charcoal bbq packing machine is a specialized…
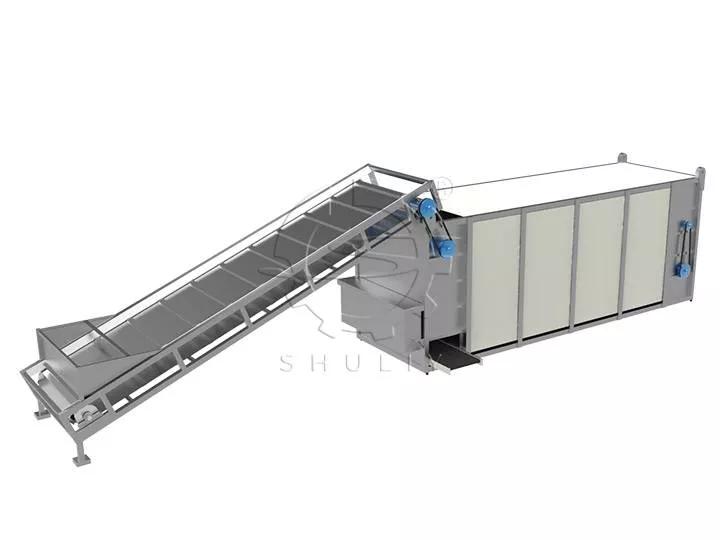
Charcoal briquette mesh belt dryer for continuous drying plant
Charcoal briquette mesh belt dryer is a continuous…
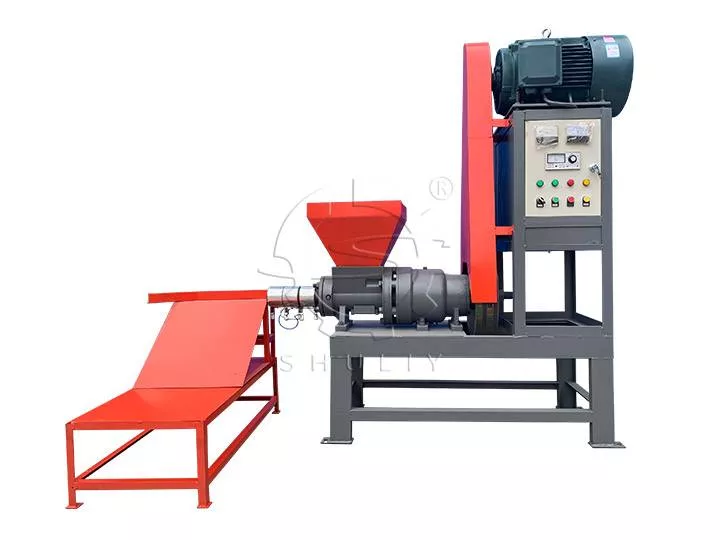
Sawdust Briquette Machine For Biomass Charcoal Processing Line
Biomass charcoal making machine can extrude and shape…
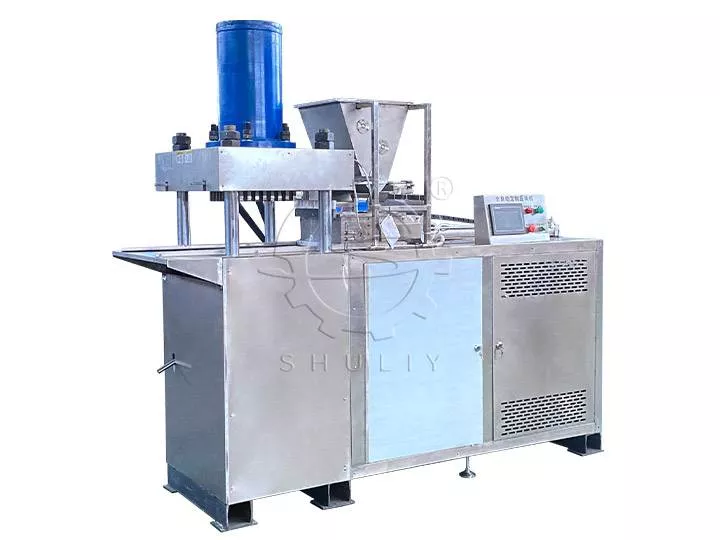
Stainless Steel Shisha Charcoal Making Machine For Hookah Briquette Tablets
The shisha charcoal making machine is also a…
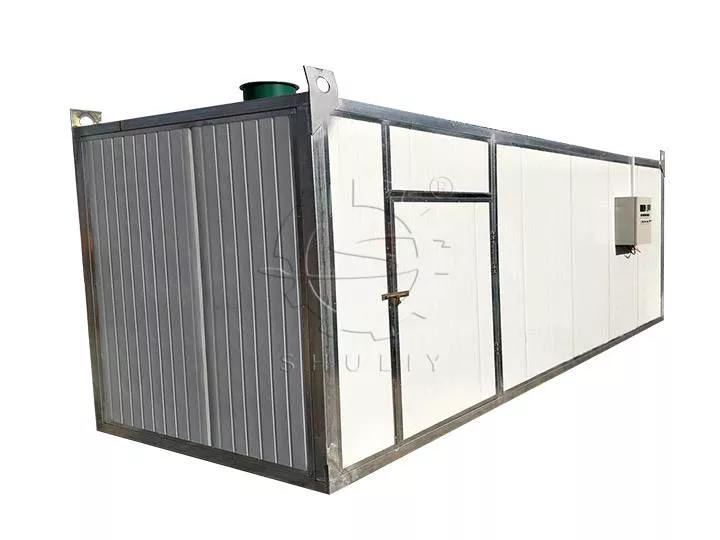
Briquette Charcoal Dryer For Honeycomb Shisha Coal Production
Briquette charcoal dryer refers to the evaporation of…
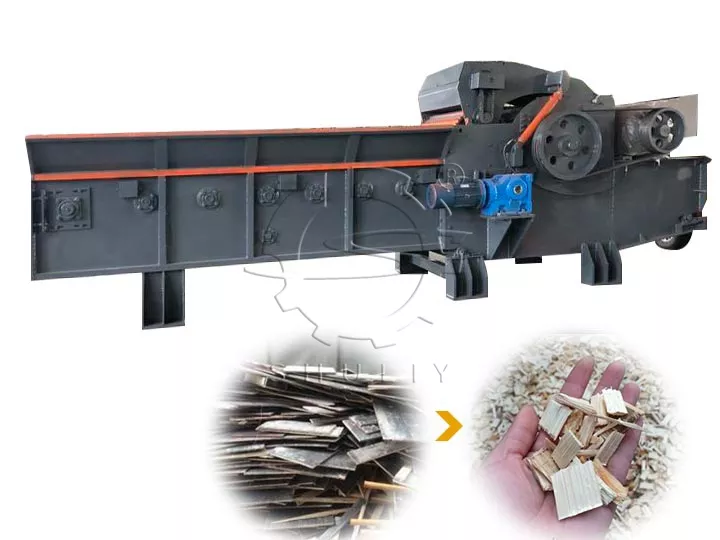
Comprehensive Crusher Large Capacity Wood Shredder Machine
The comprehensive crusher is designed to break down…
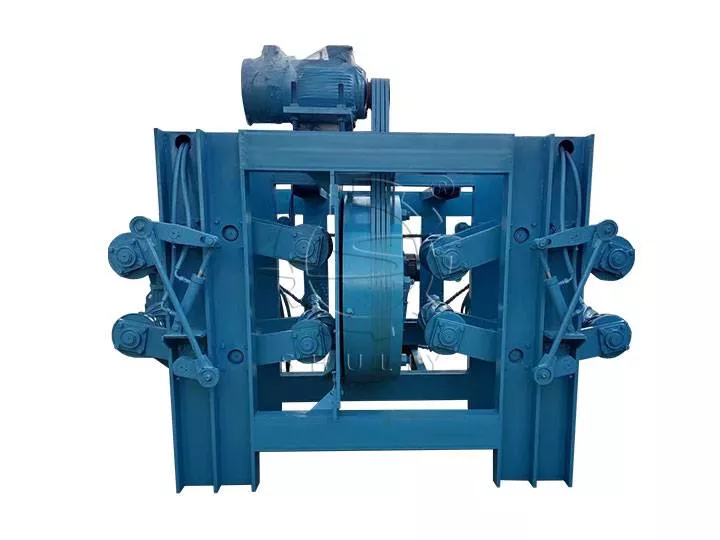
Wood Debarker Machine Timber Log Peeling Equipment
Equipped with high-strength alloy blades and advanced rotary…
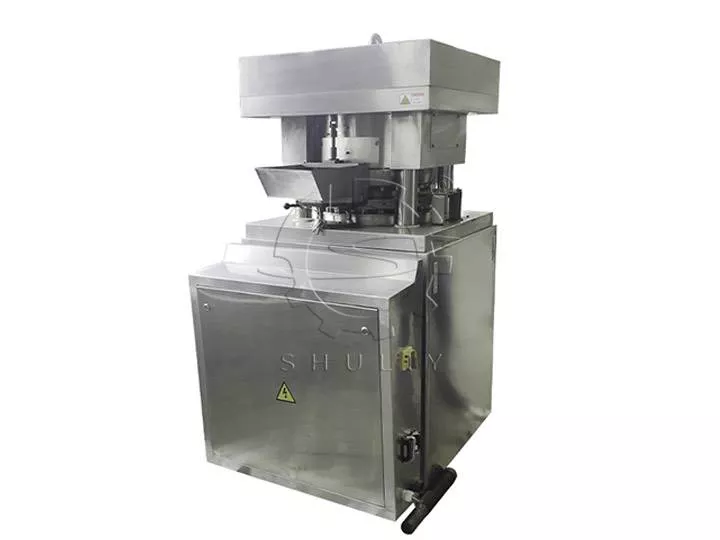
Rotary Shisha Charcoal Making Machine For Hookah Briquettes
Rotary shisha charcoal making machine is a double-press…
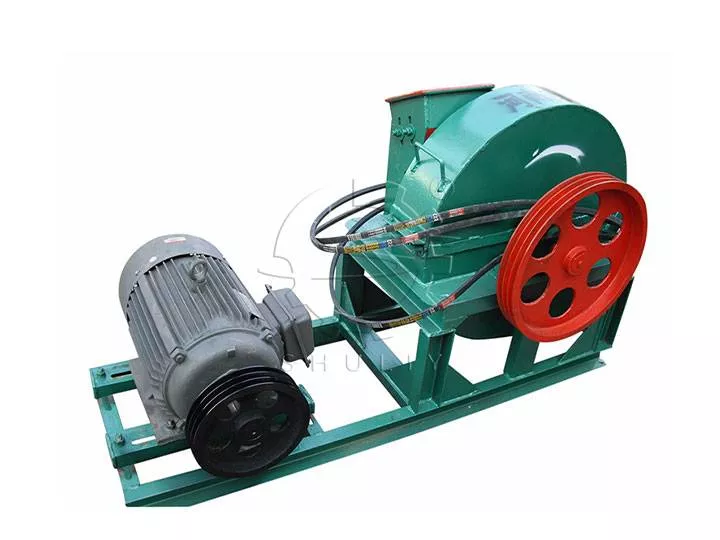
Wood Shaving Machine For Animal Bedding
The wood shaving machine is designed to process…