Precautions for the wood shaving machine use
The wood shaving machine use and shaving application is very wide. The production of shavings and hand-launched shavings are almost no different; can be used for particle board (plywood), furniture manufacturing is often used; paper mills do the raw material for wood pulp paper.
In the logistics and transportation of some fragile products to join some shavings as a filler; poultry farms are widely used as shavings as the filler in the nests of the animals; and in addition, can also be used as a bio-energy source.
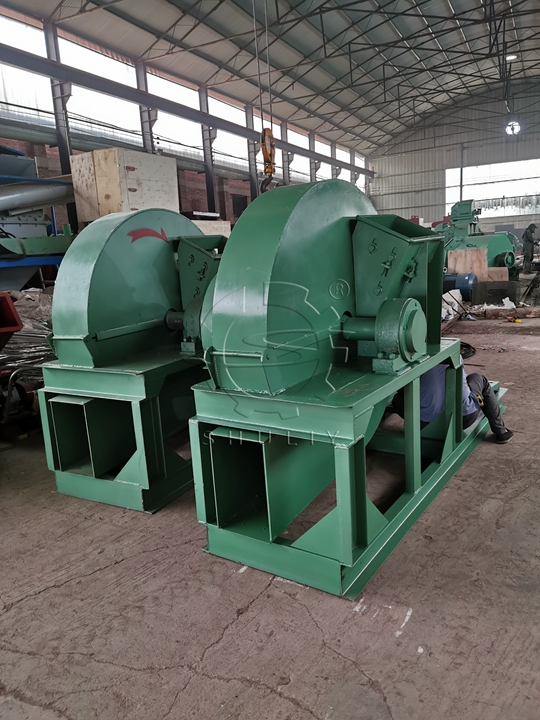
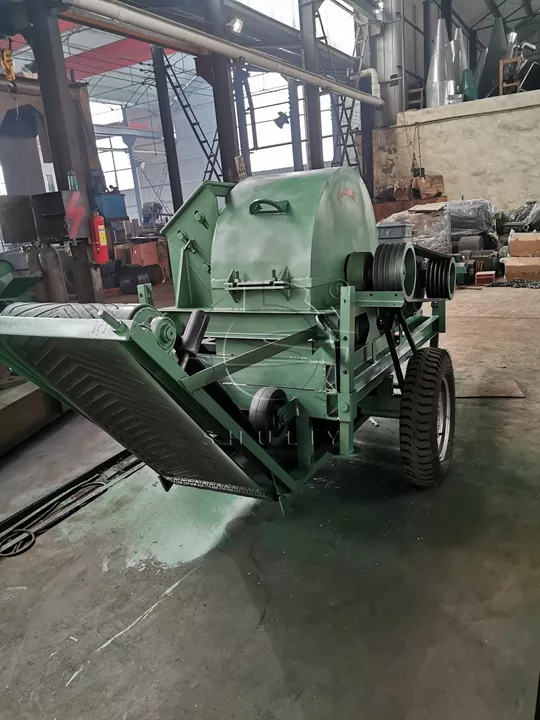
Common problems in the wood shaving machine use
- Easy to bite the belt. The reason is that the motor rotor and wood grinder rotor are not concentric, you can move the motor position left and right, or in the motor foot below the pad to adjust the concentricity of the two rotors.
- Output is relatively low. Reason: The blade is not sharp or the knife is not adjusted to the right position. Solution: Remove the knife, sharpen the blade, and adjust the blade to the proper chip-cutting position.
- Difficulty in feeding, the knife cutting chip effort. Reason: The knife is badly worn, and the clearance of the fixed knife is too big or too small. Solution: Repair and sharpen the knife blade to ensure that the blade is sharp. Adjust the clearance of the fixed knife to 2-3mm, and the angle of the blade should not be more than 30°.
- Feed too fast machine crash. Reason: When the wood shaving machine use, there is an uneven feeding speed, and the blade is not sharp. Solution: uniform feed, ensure that the crushing bin does not store material. Sharpen the blade, so that the knife cutting chip speed.
- Bearing heat. Reason: no grease in the bearing seat, the bearing seat is not mounted flat, bearing damage. The belt installation is too tight. Solution: Add grease to the bearing, balance the bearing seat, replace the new bearing, adjust the belt tightness, and make the equipment work normally.
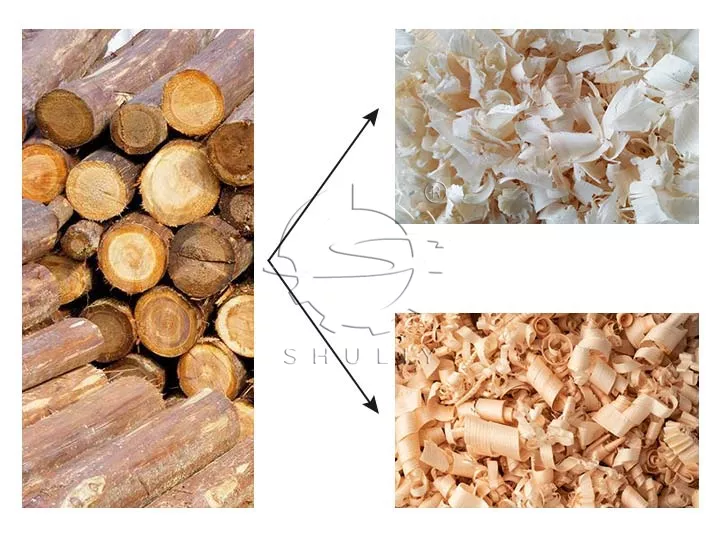
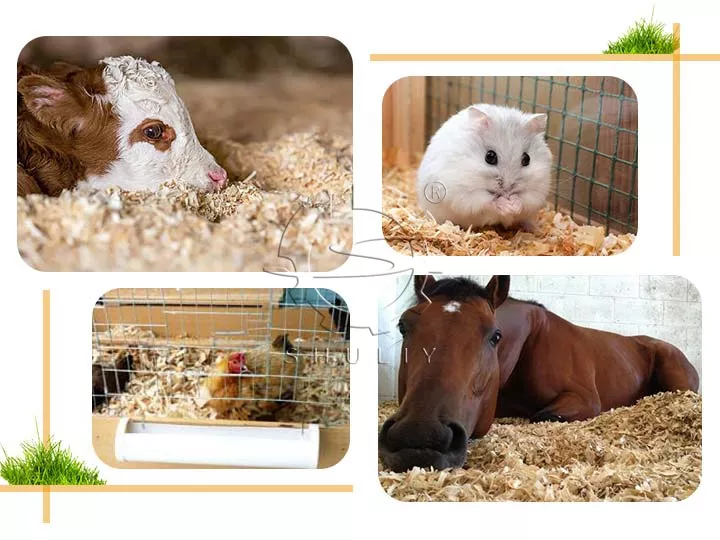
Tips for wood shaving machine use
- Adjust the tension of the belt after every day’s use, down 6-10mm suitable.
- Clean up the inside of the machine, can not leave the last crushed material.
- Bearing seat timely filling of grease, continuous work 3-4 hours to fill a grease, should pay attention to observation.