كيفية صنع فحم قشر الأرز؟ - حل إنتاجي شامل
يعد إنتاج فحم قشور الأرز مشروعًا مستدامًا ومربحًا، نظرًا لأن قشور الأرز عبارة عن مواد خام وفيرة وغير مكلفة. يقدم هذا الدليل نظرة عامة شاملة حول كيفية صنع فحم قشور الأرز، مع التركيز على طريقتي الإنتاج الأساسيتين: الكربنة المباشرة لقشور الأرز إلى فحم والكربنة متبوعة بالتشكيل في قوالب.
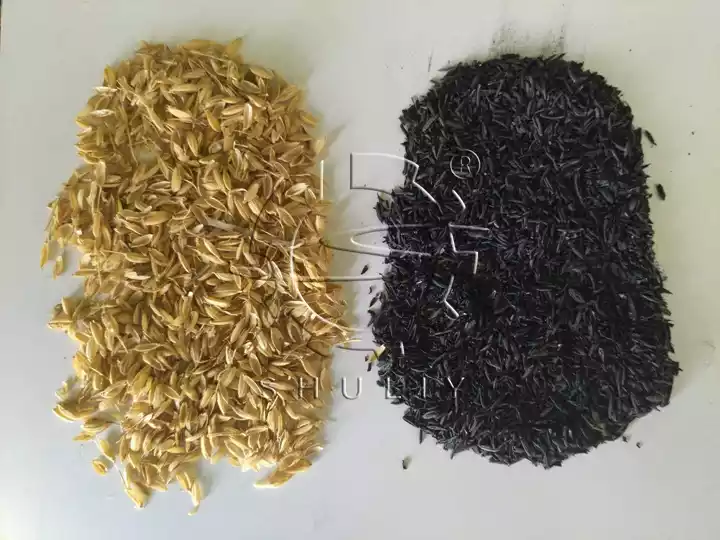
فهم إنتاج الفحم من قشر الأرز
يُشتق فحم قشور الأرز من الطبقة الخارجية لبذور الأرز، المعروفة باسم القشرة. هذا المنتج الثانوي لطحن الأرز غني بالسليلوز واللجنين، مما يجعله مثاليًا لإنتاج الفحم.
تتضمن الطريقة تسخين قشر الأرز إلى درجة حرارة أقل من نقطة الاشتعال، مما يؤدي إلى احتراق غير كامل وتكوين الفحم.
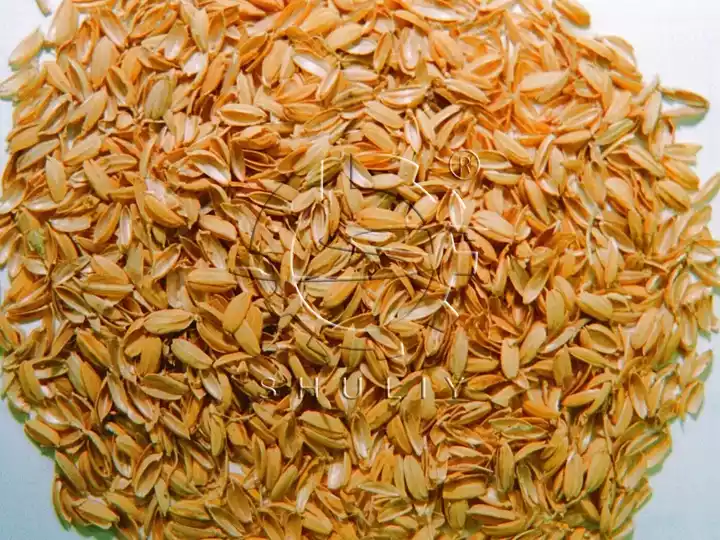
الكربنة المباشرة لقشر الأرز
التحضير والكربنة
- تحضير المواد الخام: جمع وتنظيف قشور الأرز لإزالة أي شوائب. تأكد من جفاف القشور لتحسين عملية الكربنة.
- طريقة الكربنة: للإنتاج الصغير والمتوسط، استخدم فرن كربنة، سواء كان عمودياً أو أفقياً. للقدرات الأكبر، اختر معدات فرن الكربنة المستمر. (مقال ذو صلة: فرن الكربنة المستمر لصنع فحم قشور الأرز>>)
- المزايا: يوفر هذا النهج فوائد مثل انخفاض كثافة العمالة، وتقليل وقت الكربنة، والتشغيل الخالي من الدخان، وزيادة إنتاج الفحم مقارنة بأفران الفحم التقليدية.
مرحلة ما بعد المعالجة
- التشكيل: بمجرد كربنتها، توجد قشور الأرز الفحمية عادة في شكل مسحوق. ثم يتم تشكيلها في قوالب أكبر بمساعدة آلة تشكيل الفحم، مما يجعلها أسهل في التعامل معها والاستخدام.
- التطبيقات: يستخدم فحم قشور الأرز لأغراض مختلفة، بما في ذلك كمصدر للوقود، ومواد العزل، والمساعدة في صناعة الصلب، والأسمدة، ومحسنات التربة.
لدينا أنواع مختلفة من آلات التشكيل التي يمكنها إنتاج قوالب الفحم بأشكال وأحجام مختلفة لتلبية الاحتياجات المتنوعة. (اقرأ المزيد: أنواع مختلفة من آلات صنع قوالب الفحم>>)
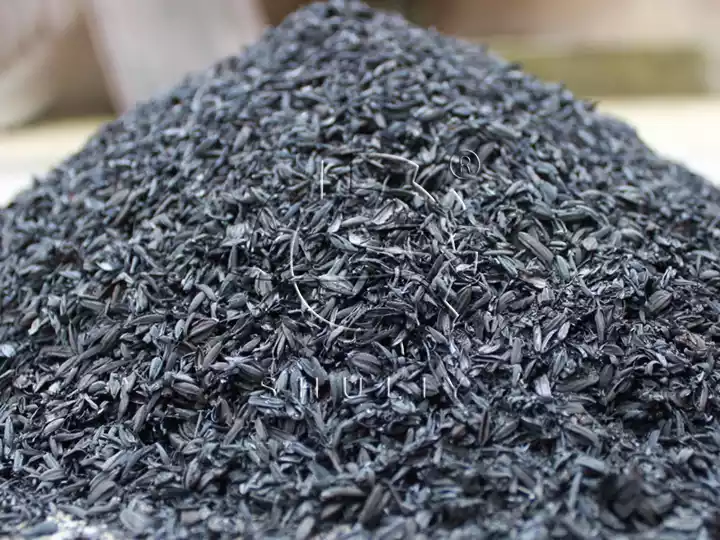
تفحيم قوالب قشر الأرز
إنتاج فحم حجري
- آلة القوالب: تم تصميم آلة قوالب نشارة الخشب لضغط قشور الأرز في قوالب دون سحقها، وذلك بفضل الحجم الصغير للقشور.
- التشكيل: يمكن لهذه الآلة إنشاء قوالب بأشكال مختلفة، على الرغم من أنها عادة ما يتم تشكيلها كأشكال سداسية أو مربعة.
- المزايا: القوالب أكثر كثافة من 1، مما يؤدي إلى عوائد فحم أعلى وينتج فحمًا نهائيًا بجودة أفضل مع تقليل محتوى الرماد والرطوبة.
عملية الكربنة
- فرن الكربنة: أدخل قوالب قشور الأرز في فرن الكربنة واتبع نفس إجراء الكربنة كما هو الحال مع كربنة قشور الأرز المباشرة.
- ضمان الجودة: تأكد من عدم إضافة أي إضافات أثناء الإنتاج للحفاظ على نقاء وجودة الفحم النهائي.
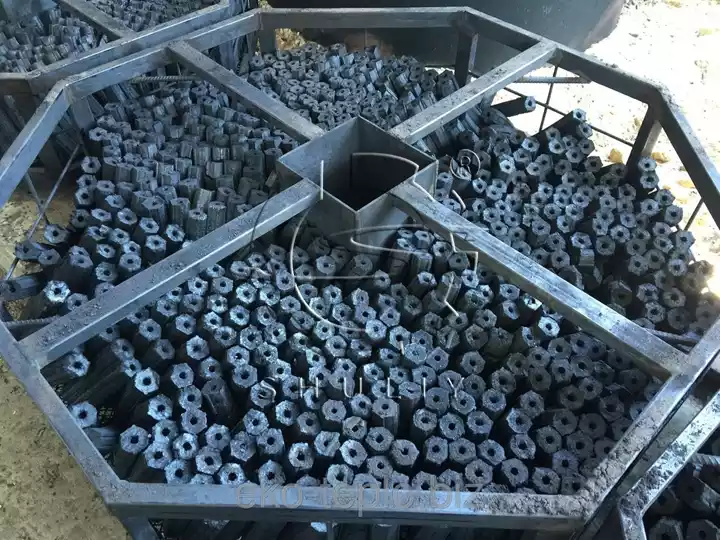
مقارنة بين عمليتي الإنتاج
يمكن للكربنة المباشرة المتبوعة بالقولبة أن تخلق أشكالًا مختلفة من قوالب الفحم لتلبية المتطلبات المختلفة. ومع ذلك، فإن السعة المنخفضة لقشر الأرز تؤدي إلى وزن تعبئة أقل لكل فرن تفحم وإنتاج أقل.
قوالب الفحم التي يتم تشكيلها أولاً ومن ثم يتم تفحيمها تظهر كثافة أعلى، ومحتوى أقل من الرماد والرطوبة، وتنتج المزيد من الفحم ذي الجودة العالية. ومع ذلك، فإن المنتج النهائي محدود الشكل، ويقتصر على الأشكال السداسية أو الرباعية الزوايا.
اختيار عملية الإنتاج الصحيحة
يتأثر القرار بشأن عملية الإنتاج التي سيتم استخدامها بعوامل مختلفة، بما في ذلك نطاق الإنتاج، والجودة المطلوبة للفحم، والطلب في السوق على أشكال معينة. توفر كلتا الطريقتين طرقًا فعالة لتحويل قشور الأرز إلى فحم قيم.
لا تتردد في الاتصال بنا لأننا نساعدك في إنشاء منتج قيم ذو استخدامات متعددة!