4 عوامل حاسمة تؤثر على جودة قوالب الفحم: ما تحتاج إلى معرفته
تلعب قوالب الفحم دورا حاسما كمصدر للطاقة اليوم، وجودتها تؤثر بشكل كبير على عوامل مختلفة، بما في ذلك كفاءة الاحتراق، والتلوث البيئي، وتكاليف الإنتاج. ستدرس هذه الورقة بدقة العوامل الأربعة الرئيسية التي تؤثر على جودة الفحم وتناقش طرق تحسين هذه العناصر لتحسين الأداء العام للفحم.
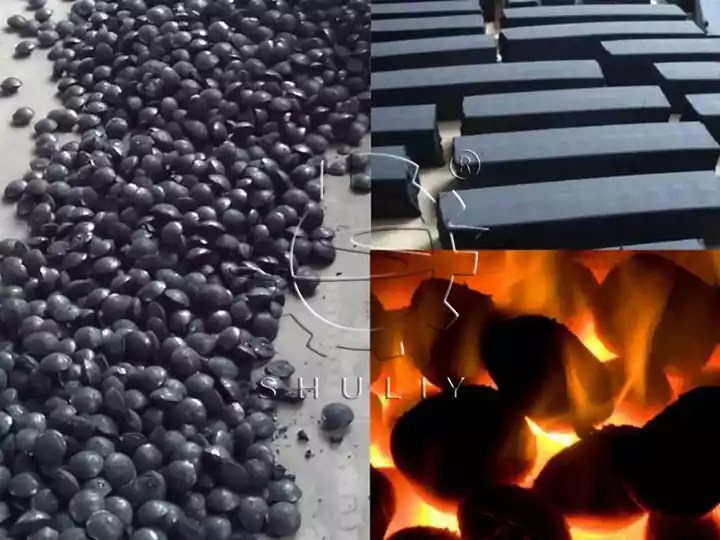
طبيعة الفحم الخام
تتأثر جودة قوالب الفحم في المقام الأول بطبيعة الفحم الخام. تلعب المؤشرات الرئيسية مثل درجة التفحم والترابط ومحتوى الرطوبة دورًا حاسمًا في تحديد جودته. تشير الأبحاث إلى أنه عندما يتجاوز مؤشر الترابط للفحم الخام 60، فإن كلاً من القوة الميكانيكية وأداء الاحتراق للفحم يتحسن بشكل ملحوظ.
بالإضافة إلى ذلك، محتوى الرطوبة العالي يمكن أن يزيد من معدل كسر الفحم أثناء عملية التجفيف، لذلك يوصى عمومًا بالحفاظ على محتوى الرطوبة للفحم الخام أقل من 10% للحفاظ على جودة مستقرة.
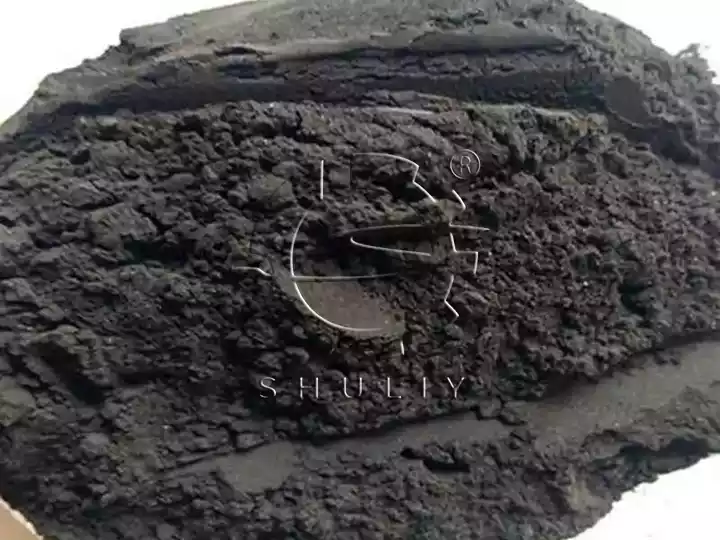
تحضير الفحم
يعد برنامج مزج الفحم المخطط جيدًا أمرًا ضروريًا لضمان جودة الفحم. ومن خلال الجمع بين الفحم الخام ذو الصفات المختلفة، يمكننا تحسين تركيبة الفحم وتعزيز أدائه. لا يؤدي مزج الفحم إلى تعزيز القيمة الحرارية وكفاءة الاحتراق فحسب، بل يساعد أيضًا في خفض التكاليف بشكل كبير.
تظهر بيانات الصناعة أن نسب الخلط الصحيحة يمكن أن تقلل تكاليف إنتاج الفحم بمقدار 10%-15% مع تعزيز كفاءة الاحتراق. على سبيل المثال، يمكن أن يؤدي مزج الفحم منخفض الجودة مع الفحم عالي الجودة إلى معالجة نقاط الضعف في الترابط الضعيف للفحم منخفض الجودة، وبالتالي تحسين قوته الميكانيكية وخصائص الاحتراق.
نوع الموثق وكمية المادة المضافة
يلعب الموثق دورًا حاسمًا في تحديد قوة الفحم ومقاومته للماء ومحتوى الرماد وكفاءة احتراق الفحم. تشير النتائج التجريبية إلى أن استخدام مادة رابطة مركبة يمكن أن يعزز القوة الأولية للفحم بمقدار 20% إلى 30% ويقلل معدل الكسر الجاف بمقدار 15% إلى 20%.
ومع ذلك، فمن الضروري التحكم بعناية في كمية المادة الرابطة المستخدمة؛ إن إضافة الكثير يمكن أن يؤدي إلى ارتفاع محتوى الرماد وانخفاض كفاءة الاحتراق بينما استخدام القليل جدًا يمكن أن يضر بقوة الفحم ويزيد من معدل الكسر.
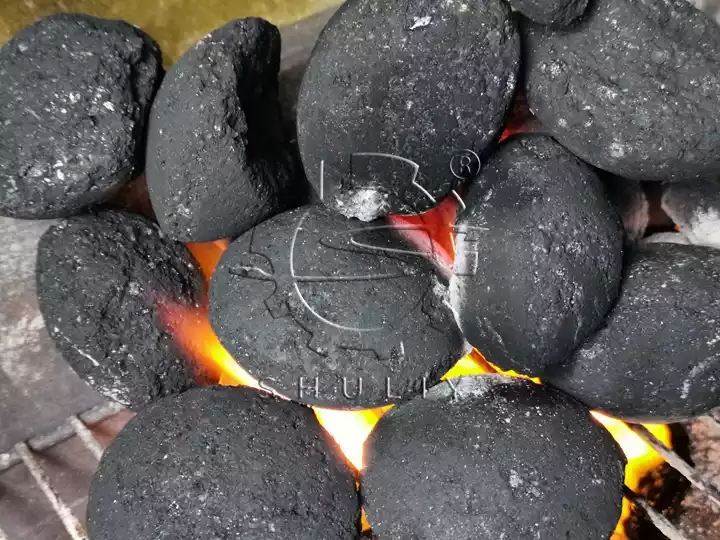
شروط صب
يعد ضغط القولبة ودرجة حرارة القولبة وطريقة القولبة من العوامل الحاسمة التي تؤثر على قوة وكثافة الفحم. عندما يتجاوز ضغط القولبة 10MPa، هناك زيادة كبيرة في القوة الميكانيكية لنوع الفحم.
تلعب درجة حرارة القولبة دورًا حيويًا في تحديد سرعة الترابط والمعالجة للفحم، مع النطاق المثالي الذي يتراوح بين 150 درجة مئوية و200 درجة مئوية. بالإضافة إلى ذلك، تنتج طرق التشكيل المختلفة أنواعًا مختلفة من الفحم؛ على سبيل المثال، قوة الفحم المنتج من خلال عملية الضغط الساخن هي الأعلى، في حين أن القوة الميكانيكية لقوالب الفحم المتكونة من خلال القولبة الرطبة أقل نسبيًا.
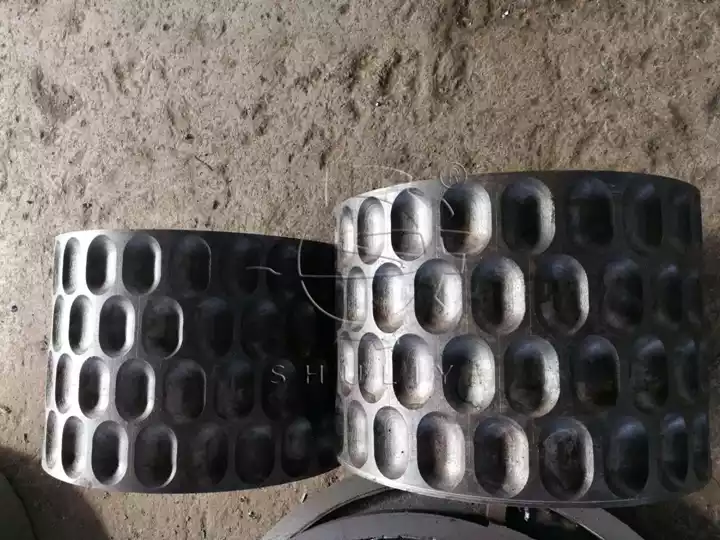
قوالب مختلفة تحصل على أشكال مختلفة من إنتاج قوالب الفحم النهائية. نحن ننتج العديد من أنواع آلات التشكيل مثل ماكينات فحم الشواء, آلات تشكيل قوالب الفحم الشيشة، وما إلى ذلك. مرحبا بكم في الاتصال بنا لمعرفة المزيد.
ومن خلال تحسين هذه العوامل، يمكننا تعزيز كفاءة الاحتراق بشكل كبير فحم مع خفض تكاليف الإنتاج أيضًا. إذا كنت مهتمًا، يمكننا توفير حل عالي الجودة لقولبة الفحم مصمم خصيصًا لتلبية احتياجاتك. لا تتردد في التواصل معنا وإخبارنا كيف يمكننا مساعدتك.