Tutorial Utama Cara Membuat Arang Batok Kelapa: Tips dan Trik Sukses
Arang tempurung kelapa merupakan produk yang banyak dicari karena terkenal akan keefektifannya, ramah lingkungan, dan kegunaannya yang luas. Ini melayani berbagai tujuan, termasuk memanggang, merokok, dan menyaring. Panduan ini menawarkan pendekatan rinci langkah demi langkah untuk memproduksi arang tempurung kelapa terbaik.
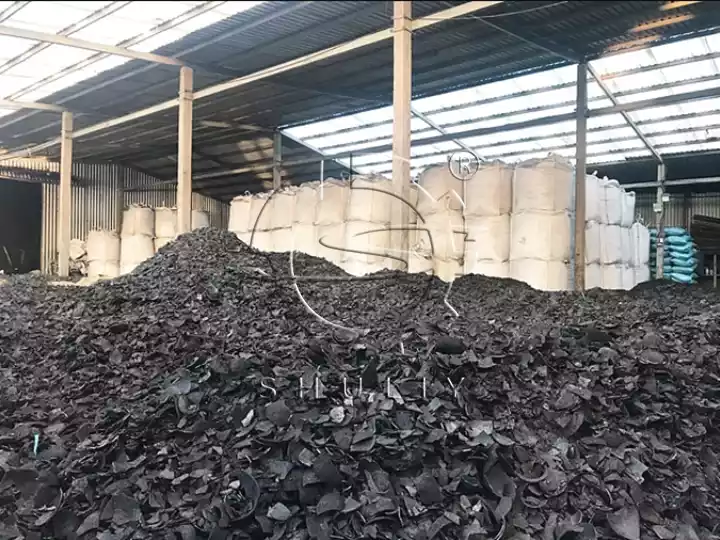
Sumber daya tempurung kelapa yang murah dan mudah diakses
Ketersediaan batok kelapa sebagai sumber daya berlimpah dan menguntungkan secara ekonomi, terutama bersumber dari pedagang kelapa lokal, pabrik pengolahan, limbah pertanian, dan pusat daur ulang masyarakat.
Di banyak wilayah tropis, tempurung kelapa sering kali dibuang setelah santan dikonsumsi, sehingga menyebabkan penumpukan yang signifikan di area seperti pasar, pinggir jalan, dan pabrik pengolahan. Kelimpahan ini memberikan peluang untuk mengakses sumber daya tempurung kelapa dengan biaya minimal.
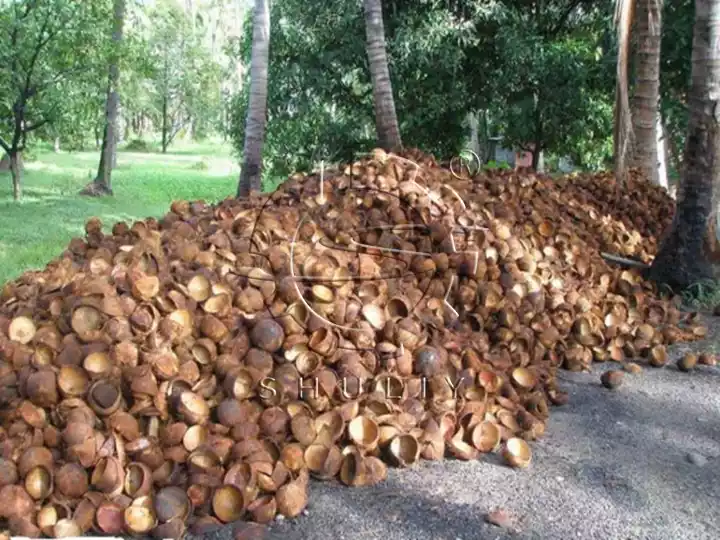
Penggunaan inovatif arang tempurung kelapa
Arang tempurung kelapa memiliki berbagai macam kegunaan, seperti:
- Memanggang dan memanggang. Kepadatan energinya yang tinggi menjadikannya pilihan yang bagus untuk memanggang dan memanggang.
- Penyaringan air. Ini berperan dalam sistem pemurnian air, secara efektif menghilangkan kotoran dan bau.
- Pemurnian udara. Arang digunakan dalam filter udara untuk menyerap racun dan bau tidak sedap.
- Amandemen tanah. Ini dapat meningkatkan kesehatan dan kesuburan tanah bila digunakan sebagai bahan pembenah tanah.
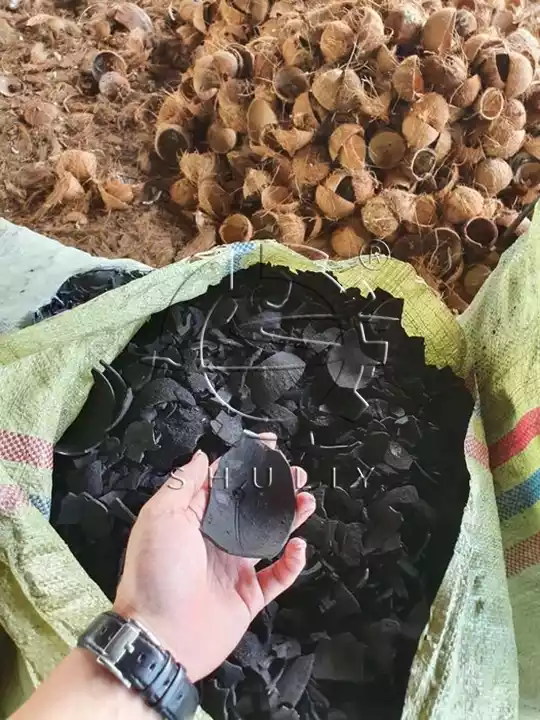
Syarat dasar pendirian pabrik pengolahan
Mendirikan fasilitas produksi arang tempurung kelapa memerlukan pertimbangan cermat terhadap beberapa elemen mendasar:
- Pemilihan lokasi yang tepat merupakan hal yang sangat penting, karena lokasi tersebut harus dekat dengan persediaan tempurung kelapa yang dapat diandalkan.
- Desain pabrik harus mencakup peralatan pemrosesan yang efisien yang mampu mengelola proses karbonisasi secara efektif sekaligus mematuhi peraturan lingkungan.
- Selain itu, mendapatkan izin dan lisensi yang diperlukan, serta berinvestasi pada tenaga kerja terampil, akan memberikan kontribusi yang signifikan terhadap keberhasilan pendirian dan pengoperasian pabrik.
- Yang terakhir, menerapkan strategi pemasaran yang efektif akan sangat penting dalam mempromosikan produk arang kepada pelanggan potensial, sehingga meningkatkan kehadiran pabrik di pasar.
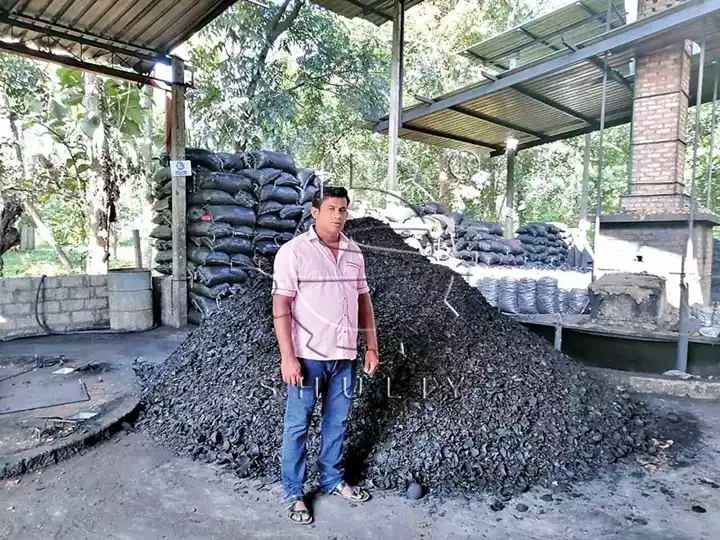
Jika Anda ingin informasi lebih lanjut, Anda dapat menghubungi kami dan memberi tahu kami kebutuhan Anda. Kami akan memberi Anda detail ini secara gratis untuk referensi.
Bahan dan peralatan
Bahan
- Batok kelapa: ambillah batok kelapa yang bersih dan kering, bebas dari sisa daging kelapa dan kelembapannya.
- Bahan bakar: ini opsional dan dapat digunakan untuk memanaskan kiln atau tungku (misalnya kayu atau arang).
Peralatan
- Kiln atau tungku karbonisasi: mengarbonisasi tempurung kelapa menjadi arang.
- Penghancur atau penggiling: penghancuran arang tempurung kelapa.
- Pabrik roda: mencampurkan bubuk arang dengan air dan bahan pengikat.
- Mesin pembentuk briket: pembuatan briket arang tempurung kelapa.
- Pengering: pengeringan briket arang.
Proses langkah demi langkah
Langkah 1: Karbonisasi
Tempurung kelapa dapat diubah menjadi arang dengan menggunakan mesin karbonisasi. Kami menawarkan berbagai jenis tungku karbonisasi, dan hampir semuanya cocok untuk memproduksi arang tempurung kelapa.
Untuk produksi arang skala kecil, Anda dapat memilih tipe kerekan atau tungku karbonisasi horizontal. Untuk pabrik arang yang lebih besar, mesin karbonisasi terus menerus akan menjadi pilihan yang lebih baik.
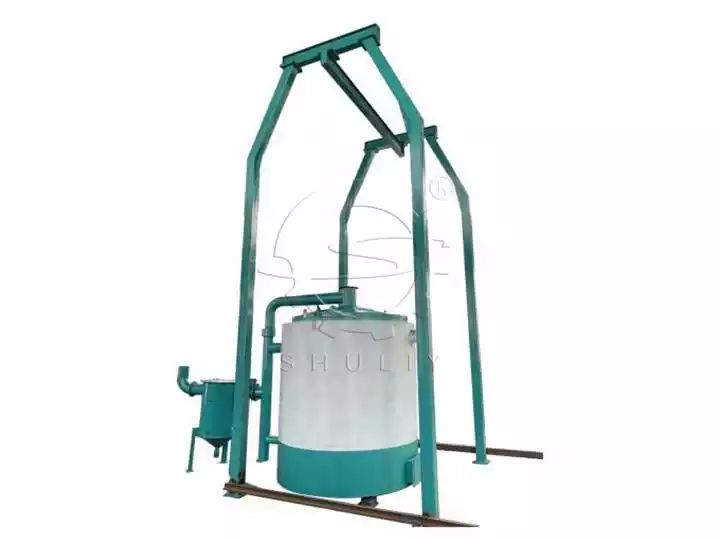
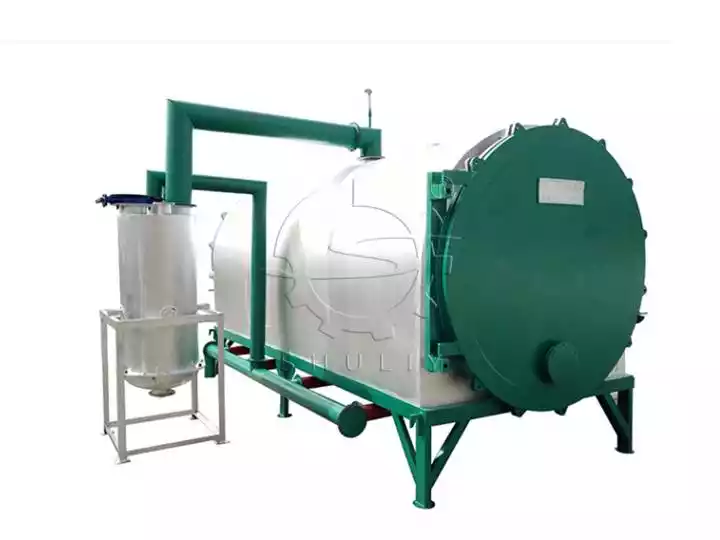
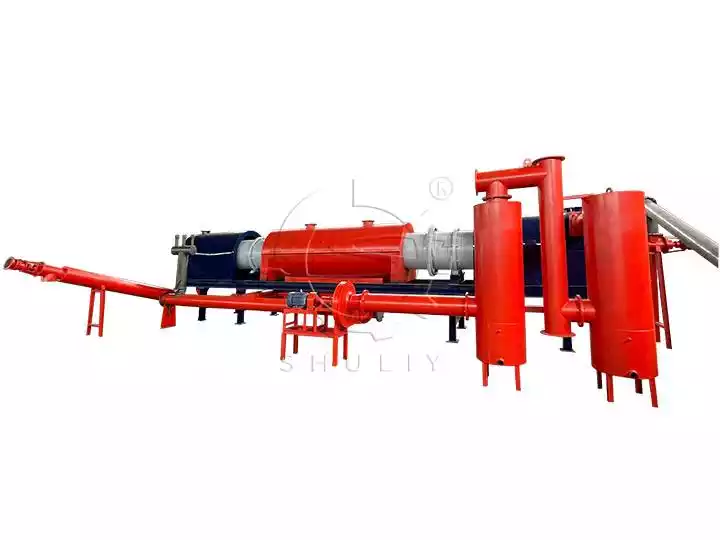
Langkah 2: Menghancurkan
Arang tempurung kelapa mempertahankan bentuk tempurungnya atau dapat pecah berkeping-keping setelah karbonisasi. Sebelum membentuk briket, arang perlu digiling hingga menjadi bubuk halus. Bubuk arang ini lebih mudah dibentuk dan membantu meminimalkan keausan pada mesin.
Langkah3: Pencampuran
Karena bubuk arang kurang kental, kita perlu menambahkan bahan pengikat untuk membantu membentuknya menjadi briket. Menambahkan bahan pengikat membuat briket arang lebih padat dan permukaannya lebih halus.
Biasanya, rasio pengikatnya sekitar 3-5%. Sedangkan untuk kadar air arang harus antara 10-25% setelah dicampur.
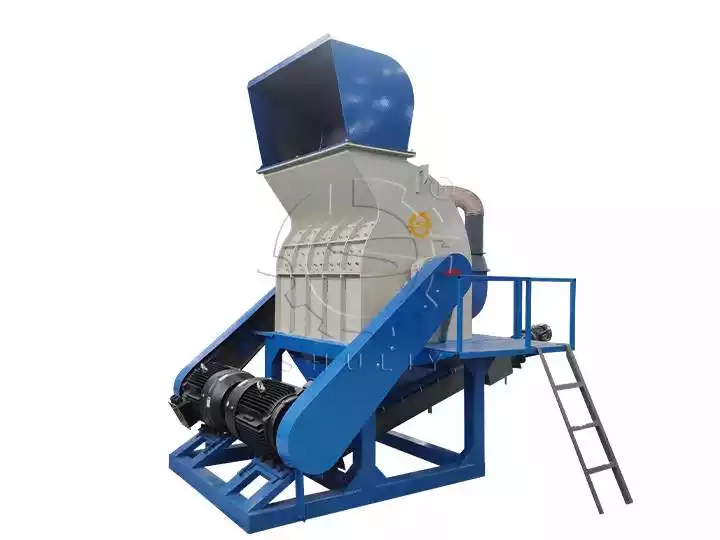
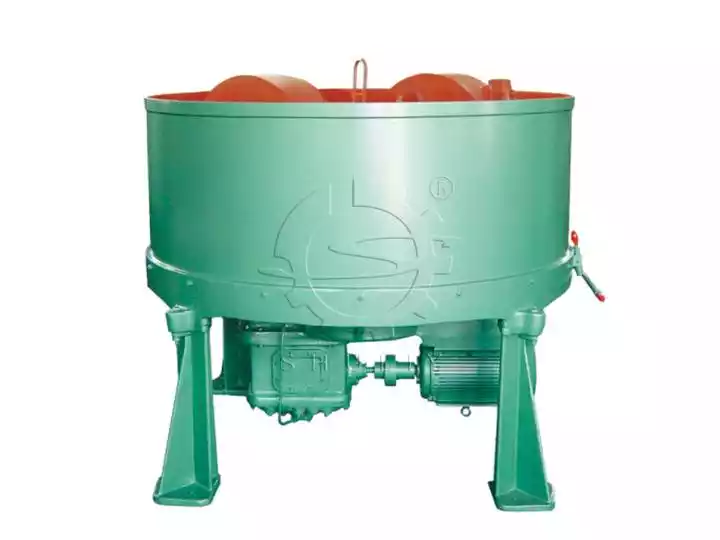
Langkah 4: Pembuatan Briket
Anda membuat berbagai bentuk briket arang untuk berbagai kegunaan, yang memerlukan mesin berbeda. Kami memiliki mesin cetak populer berikut untuk dipilih, termasuk mesin ekstruder briket arang, Mesin bola arang BBQ, mesin press arang hookah, Dan mesin batubara sarang lebah.
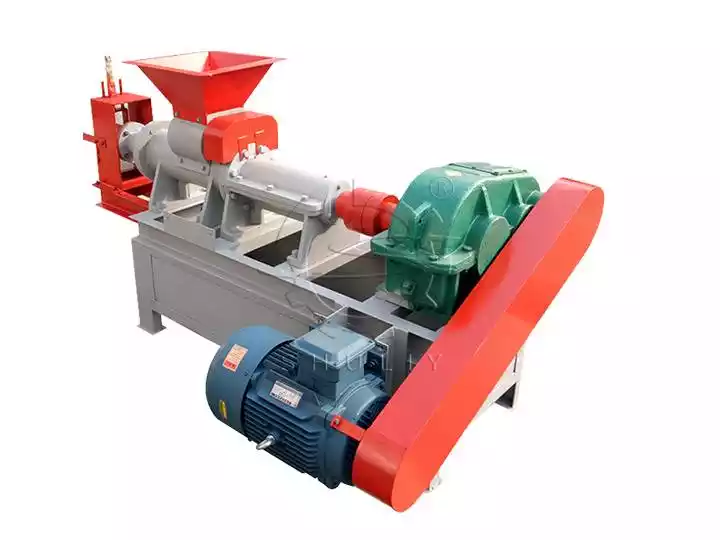
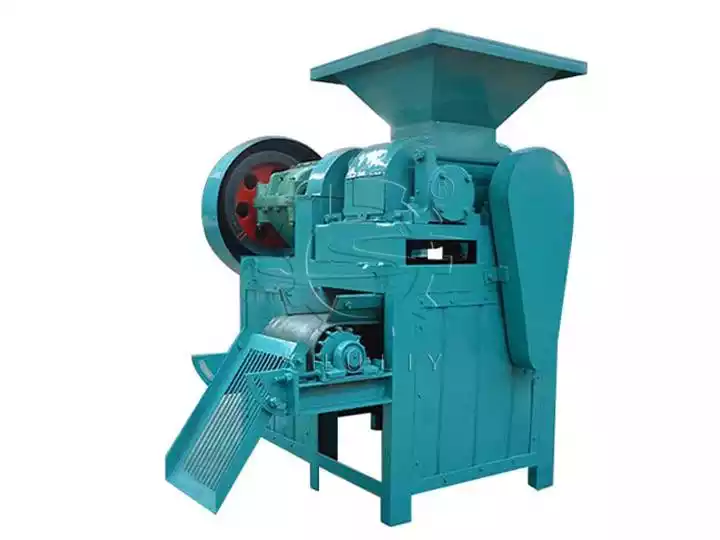
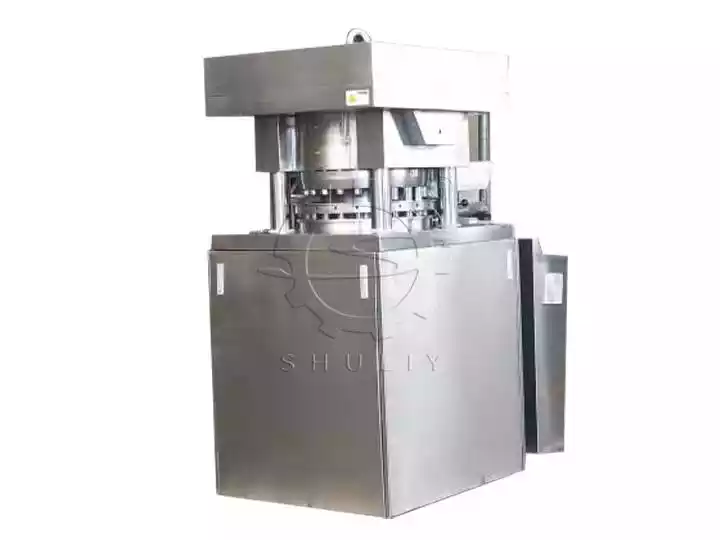
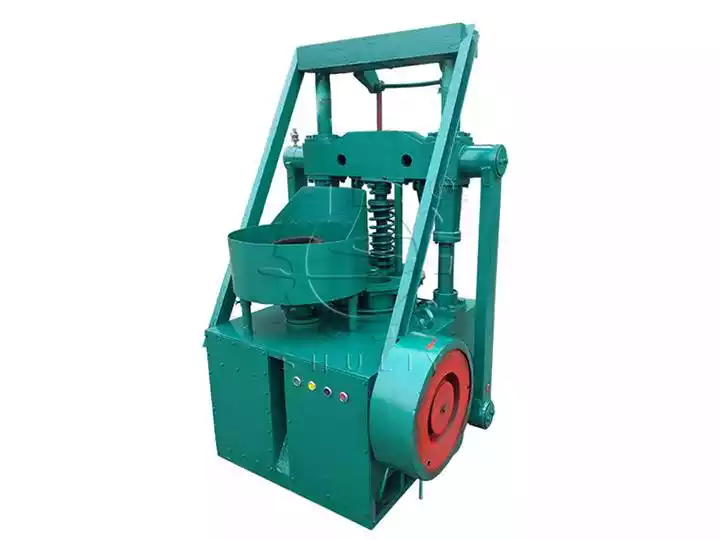
Langkah5: Pengeringan
Semua briket arang dalam keadaan basah bila diproduksi dengan mesin briket arang. Oleh karena itu, harus dikeringkan terlebih dahulu sebelum digunakan sebagai bahan bakar atau dijual di pasaran. Dibutuhkan waktu sekitar 4-7 hari untuk mengeringkan briket arang secara menyeluruh dengan cara pengeringan alami.
Oleh karena itu, kami menyarankan Anda menggunakan peralatan pengering. Ada dua jenis pengering briket arang: pengering sabuk jala Dan ruang pengering kotak, yang dapat menyelesaikan proses pengeringan otomatis hanya dalam 5 jam.
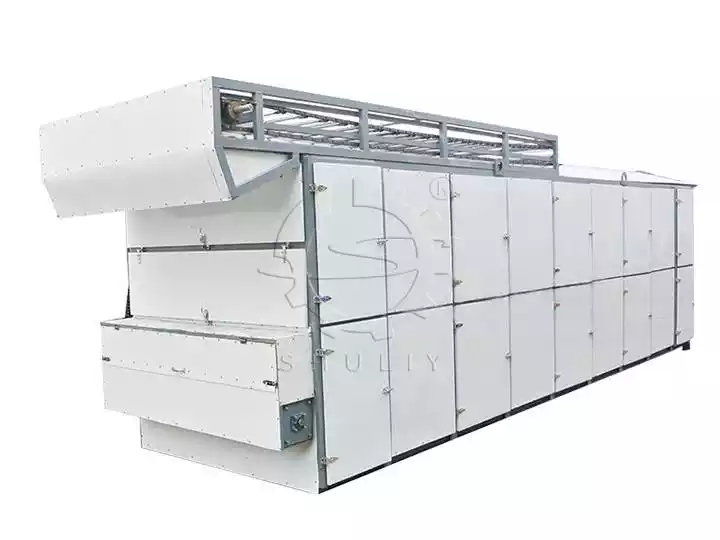
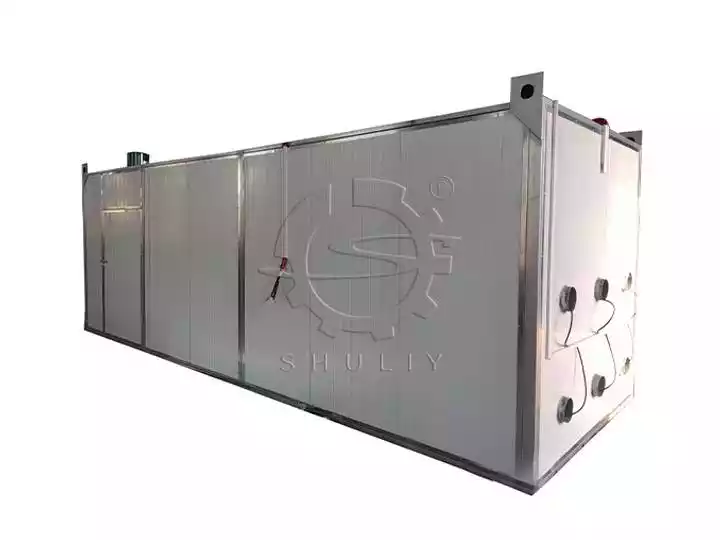
Keunggulan arang tempurung kelapa
- Daur ulang sumber daya terbarukan.
- Memiliki kapasitas adsorpsi yang tinggi dan terbakar lebih panas.
- Waktu pembakaran hingga 3+ jam.
- Abu pembakaran dapat digunakan kembali sebagai pupuk.
- Bau netral, kondusif untuk pemurnian udara.
- Berbagai kegunaan termasuk memasak, penyaringan air, dll.
Untuk mendapatkan biaya dan solusi terkini kelapa produksi arang cangkang, Anda dapat menghubungi kami langsung dengan mengisi form pesan di sebelah kanan. Kami akan menghubungi Anda kembali dalam waktu sesingkat mungkin dan berharap dapat bekerja sama dengan Anda.