Как обеспечить безопасность при производстве древесного угля?
Производство древесного угля является важной отраслью для энергетики и производства, но оно несет в себе значительные риски. Сочетание высоких температур, легковоспламеняющихся материалов и тяжелой техники требует повышенного внимания к безопасности.
Устанавливая комплексные протоколы безопасности и внедряя инновационные технологии, предприятия могут защитить своих работников и оборудование, обеспечивая при этом бесперебойную работу. В этой статье рассматриваются передовой опыт и последние достижения в области безопасности в секторе производства древесного угля.
Важность безопасности при производстве древесного угля
Процесс производства древесного угля обычно требует температуры выше 500°C во время процесса пиролиза, что представляет значительный риск. Более того, выбросы пыли и газа могут привести к проблемам с дыханием и потенциальной опасности возгорания, если их не контролировать должным образом.
Международная организация труда (МОТ) сообщает, что несчастные случаи на производстве приводят к 340 миллионам травм каждый год, причем основным фактором, способствующим этому, являются неадекватные меры безопасности.
Приоритизация безопасности работников и защиты оборудования — это не просто требование закона; это также повышает производительность и сводит к минимуму время простоя. Исследования показывают, что на предприятиях, где особое внимание уделяется обеспечению безопасности, происходит в среднем на 25% меньше несчастных случаев.
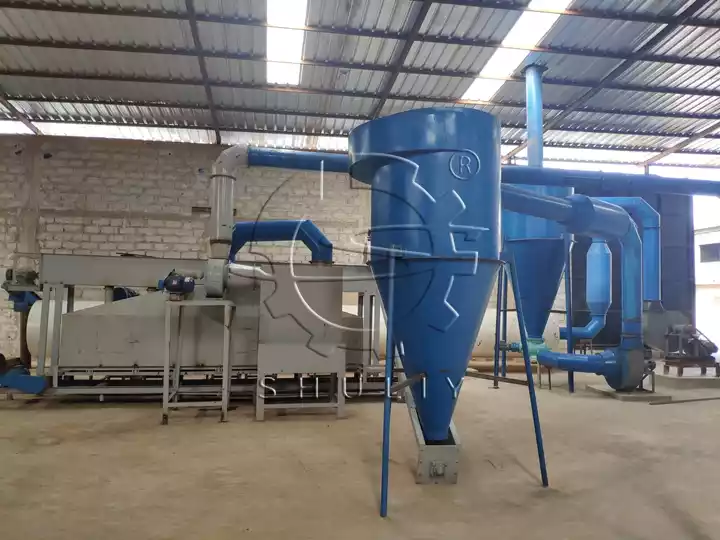
Ключевые риски в производстве древесного угля
- Опасность возгорания: наличие искр и легковоспламеняющихся материалов повышает риск возгорания.
- Токсичные газы: недостаточная вентиляция может привести к вредному воздействию угарного газа и других выбросов на работников.
- Несчастные случаи с машинами: без надлежащего обучения и мер безопасности тяжелое оборудование может быть опасным.
Лучшие практики защиты работников
- Обучение: тщательное обучение технике безопасности помогает работникам понимать потенциальные опасности и способы реагирования в чрезвычайных ситуациях.
- Средства индивидуальной защиты (СИЗ): ключевые предметы, такие как термостойкие перчатки, шлемы и респираторы, помогают снизить риски, связанные с высокими температурами и вредными газами.
- Системы вентиляции: эффективные вытяжные системы имеют решающее значение для предотвращения накопления токсичных газов, тем самым снижая риски для здоровья органов дыхания.
- Регулярное техническое обслуживание: регулярные проверки печей, конвейеров и измельчителей необходимы для предотвращения поломок и сведения к минимуму риска несчастных случаев.
- Системы аварийного отключения: машины должны иметь функции автоматического отключения, чтобы предотвратить перегрев или эксплуатационные ошибки.
Инновационные технологии безопасности угольных машин
Современные технологии революционизируют практику обеспечения безопасности в производстве древесного угля. Эти достижения улучшают обнаружение опасностей и снижают вероятность человеческой ошибки, что приводит к общему повышению безопасности.
- Сложные датчики отслеживают температуру, давление и уровень газа, предупреждая операторов в режиме реального времени.
- Автоматизация снижает необходимость прямого участия человека в выполнении опасных задач. Это не только снижает риск несчастных случаев, но и гарантирует стабильное качество продукции.
- Системы пылеподавления эффективно улавливают и нейтрализуют находящиеся в воздухе частицы, улучшая качество воздуха и сводя к минимуму риски пожара, связанные с горючей пылью.
Менеджеры по производству древесного угля должны внедрять эффективные политики и системы безопасности. Постоянно повышая осведомленность о безопасности и развивая хорошие привычки в области безопасности, мы можем обеспечить долгосрочную стабильность производства древесного угля.